PRESSURE-SENSITIVE TAPE AND TECHNIQUES FOR ITS REMOVAL FROM PAPER
Merrily A. Smith, Norvell M. M. Jones, Susan L. Page, & Marian Peck Dirda
1 HISTORY
PRESSURE-SENSITIVE TAPE—so-called because light pressure causes it to stick readily to most surfaces—typically consists of four component layers (Fig. 1). Two of these layers are readily recognizable: the adhesive mass, which is usually composed of a synthetic or natural rubber (more recently of an acrylic polymer), and which may contain a variety of softeners, antioxidants, plasticizers, and curing agents; and the backing, or carrier, which may be foil, crepe paper, fabric, cellophane, cellulose acetate, plasticized polyvinyl chloride, or any of a number of other flexible materials, and which may be reinforced with glass or other fibers. Less apparent but equally important are the keying coat, or primer, used between the adhesive and backing to insure good adhesion between the two (it may be based on natural or synthetic elastomers and may contain some tackifiers); and the release coat, applied to the side of the backing that is away from the adhesive mass, so the roll can be unwound without leaving any residual adhesive. Details about the nature of the adhesive mass and the backing are generally obtainable from the manufacturer, but components of the keying coat and release coat are proprietary information.
Fig. 1.
Four components of a typical pressure sensitive tape.
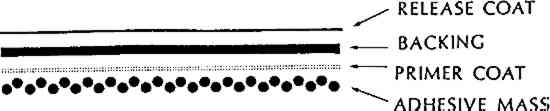 |
Pressure-sensitive tape was first developed in 1845 by Dr. Horace Day, a surgeon, who devised a method of applying a natural rubber adhesive to strips of cloth, thus producing a kind of surgical tape which he used in his practice.1
The next major application for a pressure-sensitive tape came from the auto industry in the 1920s. Two-toned automobiles were becoming increasingly popular, and manufacturers needed an efficient way to produce a clean, sharp edge where two colors met, and still maintain the production speed that had been achieved through the invention of the automatic paint spray gun. When areas were masked off with paper held in place with cloth surgical tape, the solvents in the newly-sprayed paint seeped through the cloth and caused it to stick to the surface it was supposed to protect. In 1925 Minnesota Mining and Manufacturing Company (3M) solved this problem with the invention of masking tape—a tan paper backing coated with a rubber adhesive combined with various oils and resins to make it tacky.2
From this beginning the pressure-sensitive adhesive industry began to grow. New tapes were developed and new applications for them were found. Gradually, the adhesive component was changed to synthetic rubber compounds, and a new transparent backing material was developed from regenerated cellulose, called cellophane. In the 1950s cellulose acetate and its copolymers came into use as tape backings, and synthetic polymers combined with resins came into use as adhesives. Among the first of these tapes was Scotch Brand #810 Magic Mending Tape, a matte-surface (frosty) tape that consists of a cellulose acetate carrier and an acrylic polymer adhesive.
As the development of tapes progressed and people recognized the convenience of using tape to mount, hang, and mend almost anything that came to hand, questions began to arise about the stability, removability, and long-range effects of the materials involved. In the 1970s—partly in response to demands from the conservation, picture-framing, and library communities—two companies started producing so-called “archival” pressure-sensitive tapes: Hans Neschen International developed Filmoplast P and Filmoplast P90; and later in the decade Ademco introduced Archival Aids Document Repair Tape. Filmoplast P has a relatively transparent short-fibered acid-free paper carrier, which now (but not initially) contains a calcium carbonate buffer. Filmoplast P90 has a heavier paper carrier, also buffered. The adhesive on both tapes is an acrylic ester that is laid on from a water-based dispersion. The Archival Aids Document Repair Tape also has a paper carrier that, according to the manufaturer, is made from acid-free, sulphur-free bleached wood pulp and a butyl-acrylate acrylic adhesive that contains a small amount of dibutyl-phthalate plasticizer to give it a pressure-sensitive characteristic.
The growth of the adhesive-tape industry in less than sixty years is nothing short of amazing: 3M alone manufactures 1,000 different kinds of tape that will stick just about anything to anything. The conservator's lot seems to be how to get them unstuck.
|