ON COPYING BRONZE STATUETTES
Ann H. Allison, & Robert B. Pond
ABSTRACT—In the replication of small statues by the cire perdue technique, the copies are invariably smaller and the dimensional fidelity to the bronze model is not exactly what might be expected. These deviations, the causes of which include mold shrinkage, transformation and solid state shrinkage of the alloy, are presented. The analysis of their effects upon a sound casting proves that the subtleties of replication leads to uncertainties in the ranking of statuettes in order of original and copy and that the majority of the shrinkage results from that of the alloy. With good casting procedure shrinkage limits of 2.5% to 3.18% can be expected, dependent upon the constituents of the copper alloy. Taking into consideration the deviations to be expected in each copy, a method is proposed whereby the combination of careful internal measurement of a statuette series to index statistically the degree of shrinkage with the stylistic approach of the art historian allows one to establish the chronological order of the castings.∗∗∗∗∗∗The method has been applied to replicas of a motif created by the Italian Renaissance sculptor, Antico, upon whose bronzes Dr. Allison is preparing a monograph.
1 INTRODUCTION
IT IS THE PURPOSE of this paper to present and explain the origin of some of the difficulties encountered in replicating small statues by casting as well as to establish the limits of shrinkage that can occur when a bronze casting is derived by replicating an original casting. It is our further purpose to propose a method by which the chronological relationship of a series of bronzetti of the same or of a slightly varied motif may be evaluated.
A metallic statue can be copied in at least three ways. First, if the copier is an artist gifted as a copyist, he can reproduce the form to an exactness dependent only on his skill and the opportunity to study the original carefully. His method of modeling, molding, and casting may be closely similar to that of the original artist. Second, if a part mold of the original work exists, a wax replica can be derived or a second casting be made directly into the part mold. Third, if the copier has the advantage of possessing the original work for a short period of time, during which he can generate directly from it a multipart mold, then, at his leisure, he can reproduce the work over and over again by the lost wax method.
In a discussion of bronze joining, Cyril Stanley-Smith1 said, “The greatest problem that a historian of techniques faces is, perhaps, to avoid jumping to the conclusion that an object was made in the way that he himself would find natural to make it!” The purpose of this paper is not to establish a single system of copying as optimum or even much used. It is our intent to inform those not familiar with the last of the methods mentioned above of some of the problems, results, and limitations of the technique.
2 GENERAL TECHNIQUE
THE GENERAL TECHNIQUE for generating a copy of a metal casting involves a number of steps which must be carried out in a rather exacting manner in order to produce a sound casting. It is possible to understand the reasons for the various steps by analyzing the materials changes that take place as the molds are prepared, and the alloy melted, cast, and solidified.
Step 1. The model to be copied is studied to determine the number of pieces which will be required to generate the piece mold. In this decision there are two points to be considered: 1, the number of mold pieces should be kept at a minimum and 2, no mold piece should be shaped so that it tends to retain any part of the model during separation. Step 2.The various mold pieces are cast in Plaster of Paris so that they form fits on parting lines and can be reassembled in only one way.
This is easily accomplished by encasing in soft clay that part of the model from which the first mold piece is not to be made. The soft clay can be worked to the parting line desired in a leisurely manner since it does not become hard until its water (or other vehicle) evaporates. The model is oiled, greased or waxed so that when the plaster which is cast against it hardens, it can be easily parted fromthe model and the soft clay. After the plaster of the first mold piece hardens, the soft clay encasement is removed from that part of the model to be copied by the second mold piece. The plaster of the first mold piece is oiled or greased so that the second plaster casting will not stick to it. The second piece of the mold is cast and the above procedure continued until the entire model is encompassed by the various mold pieces of plaster. These pieces are removed from the model and reassembled to form a cavity which is the three dimensional negative of the model.
Step 3. If the piece mold is to be preserved, then it is used to make a wax replica of the model. This is accomplished by filling the piece mold cavity with molten wax. The plaster must be imbibed with water to insure that the wax will not wet (or be absorbed into) the plaster. The wax will begin its solidification at the cold plaster surfaces and the solid wax will form as a shell. When this shell reaches the thickness desired by the artisan, the excess liquid wax is decanted. The plaster piece mold is removed and can be reused to make more wax replicas. The wax replica shell may be dressed of excess wax such as the flash which exists at the parting surfaces of the piece mold. It is now ready to be invested in a seamless plaster mold which will be used as a flask for the metal casting. Step 4.The plaster which will fill the inner part of the replica wax shell (the core) may need some lateral support once the wax is removed. This support is provided by pins or rods, which are inserted into the wax replica at appropriate points so that they extend from the surface and into the cavity. Rods, tubes or blocks of wax are attached to the wax replica at the point where the molten metal is desired to be fed as well as those points where there may be a gravity entrapment of gas or a sufficiently large section to sponsor internal transformation shrinkage (to be discussed later). See Fig. 1.
Step 5.The wax replica is now invested in Plaster of Paris or a mixture of plaster and some aggregate such as silica or quartz sand. After the plaster has hardened the wax is rendered from it by elevating the temperature so that the wax shell melts and flows out. Step 6.The hollow plaster flask is geometrically but not chemically ready to serve as a mold for metal casting, as it is wet and must be dried. Air drying or low temperature drying will remove only the excess water. The water of hydration must be removed by firing at temperatures in excess of 163�C. Despite the fact that the water of hydration of gypsum plaster (CaSO4.2H2O) can be completely removed @ 163�C there is the possibility of inclusion of some quantity of a compound such as limestone CaCO3 which has a higher temperature of calcining. Therefore the mold must be heated to a temperature at or near the casting temperature of the alloy to be used. These heating operations must not be carried out rapidly or the water being eliminated will convert to steam inside the mold, causing it to explode or crack. Step 7.So that the metal will begin its solidification at the mold surface, the mold must be lowered from the high temperature of calcining before the casting operation. If this cooling is carried out too rapidly, there can be a resulting cracking of the mold. Step 8.The molten alloy is cast into the mold in a continuous and rapid manner. After cooling to room temperature the investment is removed from the metal casting and it is finished by sawing off the vents, gates, pins and sprues, all of which were purposely placed, as well as any flash resulting from cracking of the mold. Fine tooling by filing, abrading, burnishing, chiseling, scraping, etc., is also necessary. This ancient cire perdue method, described in many writings, is presented in great detail by Choate.2
Fig. 1.
Illustrating the effect of solidification direction on the position of transformation shrinkage volumes.
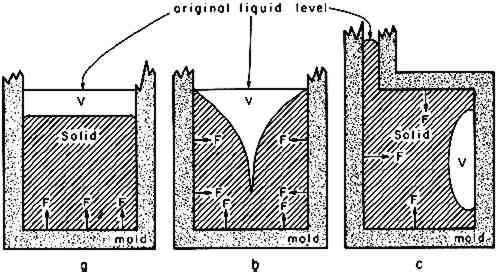 |
A good statuette copy should have dimensional fidelity to the original. However, a copy produced in a mold taken from the original model will be smaller due to the shrinkage of the metal. If such shrinkage were uniform and not affected by factors disturbing the constancy or by pre- or post-casing modification, it would be very simple by careful comparative measurement to document the original, first copy, second copy … etc. Such a documentation should still be possible in many cases if one is cognizant of the problems involved in the reproduction technique.
Offhand, one might imagine that, if this process is properly carried off, the statue will be different in dimension only by shrinkage of the alloy from its molten state to its solid room-temperature state. This, however, is not the case. The total shrinkage (ST) from the original dimensions is a function of several variables and can be represented as:
Fig. .
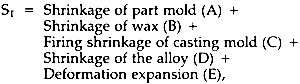 |
Neiman3 in his discussion of shrinkages and methods of compensation peculiar to copper alloys states that the caster has four types of dimensional change to consider:
Fig. .
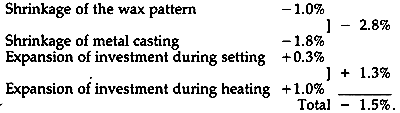 |
The expansion of the plaster during setting and heating is explained by Skinner and Philips4 as resulting from silica incorporated as an aggregate with the plaster.
A number of experiments have been carried out to determine how the shrinkages (A, B, C, D above) change with varying conditions. Figure 2 indicates that the shrinkage of the wax pattern is definitely a function of the temperature of the wax when cast.
Fig. 2.
Showing the effect of casting temperature of wax on its shrinkage.
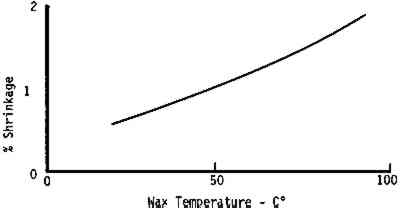 |
Figure 3 indicates that the shrinkage of the plaster in setting is a function of the water to plaster ratio.
Fig. 3.
Showing the effect of the water-plaster ratio on the shrinkage of silica free gypsum plaster.
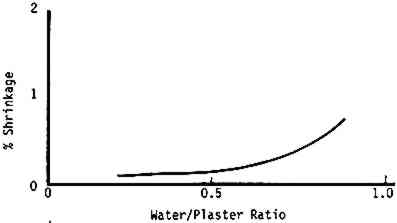 |
Figure 4 indicates that the shrinkage of the plaster on firing is a function of water-plaster ratio and the temperature of firing.
Fig. 4.
Showing the effect of firing temperature on the shrinkage of silica free gypsum plaster of the two different water-plaster ratios.
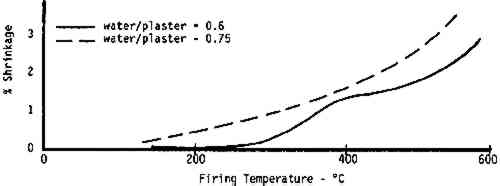 |
A good artisan would not heat the wax any higher than necessary. Overheating will not only cause excessive shrinkage but will also cause evaporation of water from the surface of the piece mold with a resulting porosity of the wax pattern. A good artisan would also avoid the use of high water-plaster ratios since excessive water will cause great shrinkage as well as cracking of the plaster flask.
In considering the shrinkage (D) of the metal, attention should be directed to the mechanism of solidification of alloys. It is not uncommon for metals and alloys in the molten state to have absorbed gasses which upon solidification are rejected from the metal. It is possible in molten alloys to have a gas generating reaction in the liquid state which continues even during solidification. Frequently, water trapped in the mold is gassified by the molten metal striking the mold. The presence of such gasses trapped in the casting are generally referred to as blow holes unless they are of very small dimension and are distributed in the dendritic (tree like) solidification pattern, when they are referred to as dendritic porosity.
A large shrinkage occurs when most metals and alloys transform from the liquid to the solid state. If this shrinkage is contained within an already solidified portion of the casting so that no liquid metal can be fed to the shrinking volume, then a cavity is formed which contains a vacuum. If this cavity is near a surface, the solid metal can be deformed inward to relieve the vacuum. These cavities are referred to as shrinkage cavities. If they are continuously connected throughout the casting, they are referred to as pipes. The shrinkage of a casting must not be confused with either the density or porosity of the casting (see Hesse 5). A casting may be only 85% dense because it contains many shrinkage cavities, blow holes, etc., and yet the shrinkage from the model may be only 2%.
A good casting will be fed during solidification by properly placed tubes and risers. Therefore the transformation shrinkage in a good casting should contribute nothing to the shrinkage of the casting. The shrinkage of a good casting comes only from the solid state shrinkage of the alloy. The casting shrinkage of the copper alloys is shown by Neiman to be contained in a narrow band. Table I sets forth an array of such values of shrinkage. These values are derived from solid state shrinkage alone. If the shrinkage of the wax pattern and the contraction or expansion of the investment were added to the values of Table I, they would be consideraly altered. A cylinder model was copied in two different brasses by the cire perdue method using no silica in the plaster. The shrinkage values obtained are 2.5% for the semi-red (5-A) brass and 3.18% for the yellow (6-C) brass.
Table I
In considering the shrinkage in the alloy as it moves from the liquid to the solid state, attention should be given to the direction in which solidification proceeds. By reference to Fig. 1-a, it is noted that, when there is a planar liquid-solid interface travelling in only one direction, the volume change differential is maintained in the last material to solidify. If the waste mold is properly gated and risers of the correct volume and position are provided, then the transformation volume change is contained in the risers and does not contribute to the shrinkage noted in the finished copy. However, if conditions are not provided for the proper direction of solidification and/or proper gate and riser techniques are not used, then the liquid-solid transformation shrinkage can be retained in the statue copy and lead to undesired, localized increased shrinkage in the copy, as seen in Fig. 1-b and 1-c. Therefore, if good practice is maintained, the shrinkage from the original model will be that generated by the wax and plaster techniques plus that generated in the solid state as the alloy cools from its melting point to room temperature.
If a solid casting or a slush casting∗ is made, solid state shrinkage proceeds uninhibited. However, if the copy is made with a thin wall by the use of a core, shrinkage of the casting is inhibited by the core. If the core has a high crushing or compaction strength, it will not yield to the shrinkage of the metal shell and will cause the hot thin metal wall to flow plastically and thin rather than shrink. In this case the apparent solid state shrinkage will be less than expected. This can be understood by reference to Fig. 5: in Case 1 the shell is deformed, but in Case 2 the core is crushed. To find the extent of upsetting or crushing, one must consider the relative coefficients of thermal expansion. If both the core and the shell (casting) had the same coefficient of thermal expansion, then the solid state contraction would be the same as if it were a solid casting or a slush casting. Each part of a statue copy may be of a different wall thickness, and thus the effect of this constraint may vary as the thickness varies.
∗A slush casting is made by filling a coreless flask with molten material and decanting after the solidified shell becomes sufficiently thick. The wax models described above are the result of slush casting of wax.
Fig. 5.
Illustrating the effect of the core on solid state shrinkage. In Case 1 the strong core causes the casting to thin. In Case 2 the core is crushed and the casting follows its normal solid state shrinkage.
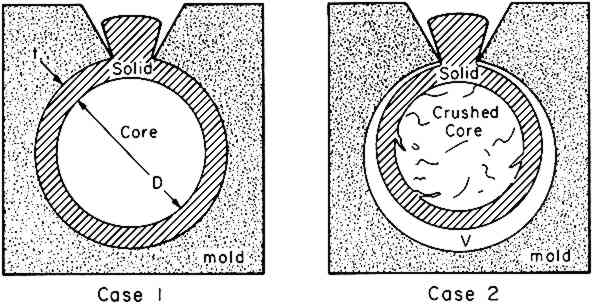 |
It can be concluded that with the qualifications given above it would be improper to make a single comparison of a dimension on a model and its copy to determine the extent of shrinkage. The best approach would be to take many measurements and make the comparison on summary basis.
3 EVALUATION OF PROBABLE COPY WORK
THE INFORMATION in the preceding sections was applied to an actual art historical case, to duplicates of a model by the Italian Renaissance sculptor Antico (c. 1460–1528). The question asked was whether the duplicates of one of Antico's motifs for statuettes were from the same mold or model or were casts taken from bronze models. If the latter were found to be true, at what removal from the autograph bronze (that is, a bronze whose modeling and casting were performed by the artist himself) are the copies? This information, obtained by the IM (Internal Measurement) method to be explained be low, permits the formation of a genealogical tree whose root is the original wax model bythe artist. Except for selected data which further clarify the stylistic characteristics of a bronze by Antico and the relationship of the bronzes to him or to his shop, a more complete art historical and technical discussion of each object has not been considered relevant to the purposes of this article.
In the determination of relative sizes of duplicate bronzes simple measurements of height have not proved reliable as they can be altered before and after casting. The IM method uses other external measurements, here called internal measurements, which are taken with a caliper. Internal measurements are those of the length, width, and depth of various parts of a statuette. The locations or stations of the parts selected for these measurements were those which are considered to be least subject to change. These stations are standardized so that they can be duplicated for each specimen of the series. As the amount a cast from another bronze shrinks is small, as many as thirty measurements are taken of each statuette in order to have a sufficiency of data. In the final analysis, with increased knowledge of the technical aspects of the bronzes studies, questionable stations are eliminated. For instance, in the case of Antico, radiography has shown that his procedure frequently involved the joining of cored limbs in the final wax model. Consequently, those stations in which this might prove to be the case were deleted. During the course of the study it was observed that measurements of length and of the head are somewhat less reliable than those of width and depth and that an ideal study should include as many of the latter types as possible. Those of length can be affected by cumulative “events” of each casting process, while the head frequently has a wall thickness appreciably differing from that of the body, thereby altering the amount of shrinkage. If the neck becomes blocked, the dimensions of the head will change due to deformation shrinkage.
The raw measurements at each station for a series of three statuettes of Young Hercules are given in Table II. In Table III these measurements are arbitrarily converted into decreasing multiples of 1.25% from that of the largest measurement at each station, so that 1 equals the standard, 2 equals 1.25%, 3 equals 2.5%, and so on. Where measurements are halfway or less between percentages, the lower multiple is chosen. In Table IV these measurements are compared on a statistical basis. As it cannot be expected that all dimensions of a bronze will correspond exactly to those of another bronze, even those of the same edition, the percentage a bronze is removed from the largest member of the series at one-half or more of the measurements is taken to be the relative size index. A line has been drawn under this number. At this point in the procedure, in order to obtain additional confirmation of the results, Table III is reviewed to ascertain which types of stations contributed to these indices. When there are more than two members of a series, a statistical comparison is made using successively smaller specimens as standards for the remainder of the series, ending with pair comparisons of each member which has not yet been directly compared. These pair comparisons in longer series involving bronzes which vary more than those illustrated here may yield unsuspected relationships between its members. The statistical results of a comparison of this type are shown in Table IV-B.
Table II Young Hercules: Internal measurements in cm. for each station; 1, w, d = length, width, depth.
Table III Young Hercules: Extent of removal from large measurement at each station—in multiples of 1.25%
Table IV Young Hercules: Statistical compilation illustrating the number of stations displaying the relative shrinkage positions in Table III
To determine whether a bronze was cast from another bronze, the average shrinkage for both red-pink and yellow alloys (discussed earlier) are taken as standards. For those bronzes cast in reddish to pink alloys a midrange shrinkage of 2.5% is used, for those in yellow alloys, 3.18%. In general, and when the alloy color is in doubt, the data is interpreted broadly. Using the results of the data gathered, a genealogical chart of a series of bronzes may be formed as in Table V.
Table V Young Hercules: Genealogical Chart
4 THE YOUNG HERCULES BY ANTICO
THREE STATUETTES of Antico's motif of Young Hercules are extant. The Young Hercules in the J. N. Jantzen collection (Fig. 6) in Bremen displays the virtuoso modeling and technique found in the best bronzes by this artist and, correspondingly, can be assumed to be autograph. The body forms of this statuette are plastic, generalized, and chased and polished until smoothly sensuous. Concern with texture is evident. Characteristic meticulously executed details include the ringlets of the hair, the small mouth, and the tiny nails on the hands and feet. Two other examples of lesser quality are in the Louvre (Figs. 7, 8). One of the Louvre bronzes differs significantly in internal measurements from the other and from the Jantzen bronze. Here the larger Louvre figure shall be referred to as Louvre A and the smaller as Louvre B.
Fig. 6.
Young Hercules, J. N. Jantzen Collection, Bremen.
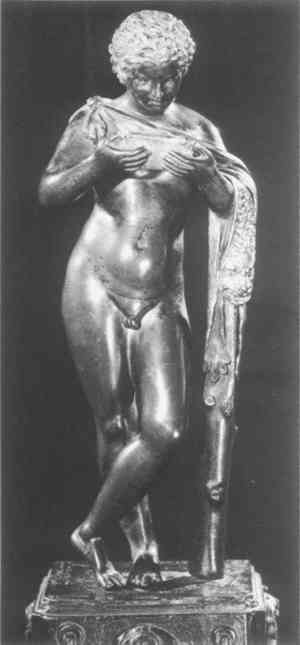 |
Fig. 7.
Young Hercules, Mus�e du Louvre, Paris (Louvre A).
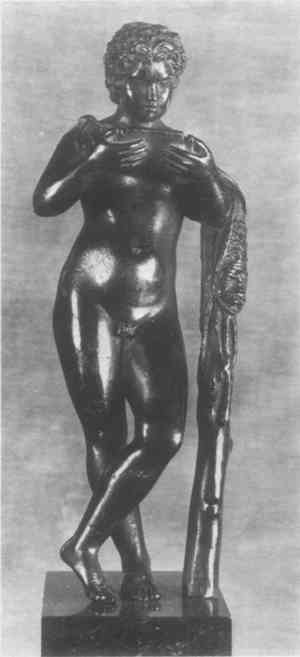 |
Fig. 8.
Young Hercules, Mus�e du Louvre, Paris (Louvre B).
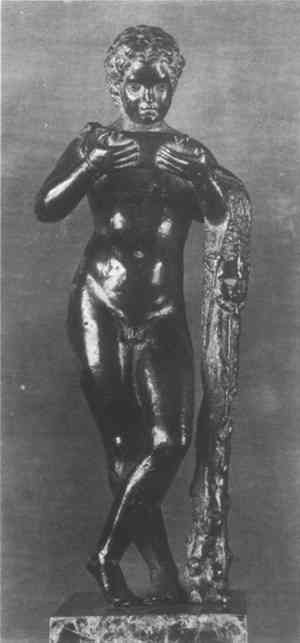 |
The application of the IM method which produced Tables II to IV has been discussed. The statistical data shows that the majority of measurements of the Jantzen bronze and Louvre A are either equal or differ by only 1.25%. Comparison of the individual stations shows that width and depth measurements of the body are either equal or differ by 2.5%, and that measurements of length and of the head deviate 1.25% to 3.75% and, in one case, 8.75%. The sum of the data indicates that Louvre A is from the same model or mold as the Jantzen bronze. Louvre B is 7.5% removed from the Jantzen bronze for the majority of the measurements, but the relative size index is 5% in the pair comparison with Louvre A. The smaller deviation from Louvre A is to be expected, for Louvre A is not so large as the Jantzen bronze at a majority of stations.
The alloys of all figures appear to be reddish. Applying the 2.5% shrinkage for red-pink alloys, it is established that Louvre B is approximately twice removed from both the Jantzen bronze and Louvre A. As both the Jantzen figure and Louvre A originate from the same model or mold, these are considered to originate in Antico's workshop. Similar to the autograph Jantzen Young Hercules, Louvre A has relatively slender core pins which are usually characteristic of Antico's casting procedure, but, as the rendering of its details is harder and the technique not virtuoso, it is presumably produced by a shop member. Louvre B is by another artist and produced at a later date, as time must be allowed for a cast twice removed from the first edition. Its artist used larger corepins and a core support at the crown of the head. All details of this statuette are softer and some differ from those of the two other specimens. Its once black patina, which has gritty material in the crevices, suggests that it was intended to pass as an antique bronze. The ultimate model of this bronze could be the Jantzen figure as that bronze has had a part-mold made of it. Incisions where one would expect divisions of a part-mold to be found may be seen cut through the patina of this bronze into the raw metal.
5 SUMMARY
THE APPLICATION of the IM method here has been to a relatively straightforward example. Within less obvious series of bronze duplicates and variants it can make a substantial contribution through the determination of interrelationships. In the use of this method photographs cannot be substituted for the object itself as variables in the measurements are introduced and much technical and stylistic data is indiscernible. A group of bronzes is best examined at each location by the person conducting the research. This study has been presented with the realization that bronze casters at any point in time do not cast alike, but have their individual procedures. In this respect, care must be taken that knowledge of modern foundry methods does not lead to improper association with bronze casting practices in other periods. More intensive technical studies, especially that of radiography, will continue to reveal the “secrets” of each casting and the procedure of the artist or shop, thereby refining the results attainable by this method alone. The IM method cannot hurt a bronze, simple measurements of height are unreliable, and no other method is currently available which is applicable to the formation of a genealogical tree of castings related by motif which were fabricated before modern times. These specimens are rarely untouched duplicates of documented models. Combined with the art historical approach, the method widens the areas of cooperation between the conservator and the art historian as it assists in the question of aftercasts, fakes, and dating and in the identification of artist and workshop.
ACKNOWLEDGEMENTS
A STUDY OF THIS TYPE could only be made with the generous cooperation of museum personnel and collectors. We wish to express our deeply felt appreciation to Johathon Ashley-Smith of the Victoria and Albert Museum, Bertrand Jestaz, Amori LeF�bure, and their associates at the Mus�e du Louvre, and to Magdalene auf der Heyde and her family.
REFERENCES
Stanley-Smith, Cyril. A discussion on “Bronze Joining: A Study in Ancient Technology,” Art Technology, edited by S.Doeringer, D. G.Mitten and A.Steinberg, MIT Press (1970)
Choate, Sharr. Creative Casting, George Allen and Unwin Ltd., London (1966)
Neiman, Robert. “Production of Finished and Semifinished Copper Alloy Castings,” ASM Handbook (1948)
Skinner, E. W. and R. W.Phillips. The Science of Dental Materials, W. B. Saunders Co., Philadelphia (1960)
Hesse, A. H. “Defects in Bronze Castings: Their Cause and Cure,” Trans. AFS, Vol. 82 (1974)
Section Index |