LEAF CASTING ON THE SUCTION TABLE
Robert Futernick
ABSTRACT—Modification of the “leaf casting” technique for use on the vacuum suction table is described. A plastic container, placed above an area of missing paper, holds water and pulp until suction is applied from below. Fibers, pulled evenly into proper position, bond with the edge of the original sheet. Prints or drawings that exceed the size of the suction table may still be treated. Through localized wetting or the use of alcohol as the casting liquid, certain problems associated with water soluble media and standard casting procedure can be overcome.
THE BEST REPAIR of paper with losses or tears requires a technique that is appropriate to the particular qualities of a paper, including consideration of intended use of the item. For example, a hole in a book page could be filled with strong, flexible Japanese paper to accommodate handling. The same hole in a master drawing would have different repair requirements, since minimizing the visual effect of damage would be of greater concern. The availability of a growing number of repair technologies enables the conservator to meet the needs presented by particular problems. Some repair methods are as old as papermaking itself, while other techniques have evolved during the last 30 years. Modification of the “leaf casting” technique for use on the vacuum suction table offers a new refinement for repair and is the subject of this paper.
Historically, filling holes with similar paper has been the most frequently used repair method. It can work well, but success will depend on adequate time to do the task, a good selection of repair papers, a minimum of edge discoloration, and the skill of the conservator. Problems can develop, however. Secure joining of the insert to the original may be difficult, especially with thick, brittle paper. Also, distortion of the original sheet can develop because of the different expansion characteristics of the two papers or the introduction of adhesive necessary for joining the insert.
Because of its strength and flexibility, Japanese paper has been widely used for book leaf repair. Two or more thin sheets laminated together and slightly overlapping the original can create an excellent fill. Though different in color and texture from many Western papers, Japanese paper inserts often provide a sympathetic match. This method seems to have less propensity for paper distortion than other techniques. Furthermore, the strain of attachment is spread over a larger area. This may be extremely important when the edge of the original sheet is weak or the intended use of the material involves extensive handling.
1 LEAF CASTING
IN THE LATE 1950s, Esther Alkalay and Ulia Petrovna Nyuksha began experimenting with the concept of filling missing areas in paper with fibers suspended in a liquid medium. By 1961, equipment for this purpose had been developed and was in use in laboratories located in Eastern Europe and the U.S.S.R. The process has come to be known as “leaf casting,” and is best described in the preprints of the 1980 Cambridge Conference (see bibliography). Today the Library of Congress and the Northeast Document Conservation Center both use leaf casting machines based on Alkalay's design. Other models, varying in cost and sophistication, have been developed in recent years and are in use in laboratories throughout the world.
1.1 Steps of traditional leaf casting
- The damaged paper should be thoroughly wet. (Extending the soak time and increasing the wetness of the sheet aids in later bonding.)
- The paper is placed on a permeable surface at the bottom of the leaf casting tub. A hold-down mechanism is usually employed to restrict movement of the damaged sheet when water is added to the area above the paper.
- A precise amount of pulp of appropriate fiber type and color is stirred into the water bath. It is important that measurement of the missing area and paper thickness be accurate and the pulp addition be correct so that the cast fills will equal the thickness of the original paper. Simple graph paper or a planimeter can facilitate this calculation.
- Suction, whether from an electric pump or gravity, is applied to the space below the damaged work. Water in the top portion drains through the voided spaces only, depositing an even layer of pulp across the loss.
1.2 Characteristics and Qualities of Leaf Casting
Leaf casting has distinct advantages over other methods of filling losses. If one's work is organized and equipment is properly adjusted, damage to paper can be repaired very quickly. It is possible to create a smooth, flexible and unobtrusive transition from the fill to the original paper. And if fibers of similar dimensional characteristics are selected and prepared, distortion can be minimized or avoided. However, there are areas of concern and potential problems in leaf casting, and they should be understood in order to take full advantage of this technique.
The bonding of the fill material to the old paper can be problematic. The quality of connection will depend on a) the state of deterioration of the original sheet; b) the bonding characteristic of the pulp prepared for casting; c) the edge of the loss and the degree of fiber extension; and d) the speed that water drains through the losses.
In the past, various kinds of adhesives have been added to the casting liquid to improve bonding. Unfortunately, adhesives affect the entire object during the period of immersion and drainage, not just the fill. This changes the nature of the paper—at the very least—and if the adhesive material proves to have poor aging characteristics, the entire artifact will suffer. Therefore, the addition of adhesives, though helpful in bonding, should be carefully considered and avoided when possible.
Conventional leaf casting requires the complete immersion of the paper in water. Clearly, many items cannot undergo this action without risking loss or alteration of the media. As a remedy, application of fixing agents has been suggested. However, it seems imprudent to impose such an altering measure just for the purpose of repair when other satisfactory methods are available. Hand pulp technique and localized leaf casting methods do not require total water immersion.
During leaf casting, there is some pulp deposition onto the surface of the original paper. As the fluid level in the tank gets low during the final stage of drainage, some of the fibers in the solution will become affixed to the surface of the original. This may be minimized if the pulp-in-fluid concentration is kept low, though in certain cases some cleanup may be necessary. (If the work is one-sided and the casting takes place with the work face down, then slight deposition on the verso may not be an issue.)
In an early publication too obscure to remember, reference is made to the employment of chronic gum chewers for major restoration ventures. Here, beating and fibrilation of fibers with cuspid and molar action is gentle but thorough, with chemical processing provided by enzymatic mechanisms (spit). Unfortunately, with leaf casting activity on the rise, it has become more and more difficult for conservators to locate eager chompers to fill increasing demand.
Many conservators have turned to the use of household blenders for conversion of old paper to pulp. Recently, blender preparation has been criticized in the literature in favor of beating devices especially designed for the purpose. Certainly, beating machines do provide precise control over fiber length and hydration and they will accommodate the use of raw fibers. Petherbridge points out that bonding and dimensional stability is very dependent on pulp quality and preparation. However, the use of expensive equipment is not always practical or necessary. If care is shown in the selection of paper for repulping and the fiber-to-water ratio is properly controlled during beating, the quality of blender-beaten fills may be acceptable for many purposes.
2 HAND PULP TECHNIQUE
HAND METHODS for filling losses with paper pulp have been in use around the world for a long time. Keiko Keyes outlined her technique at the AIC Conference in Dearborn in 1976. She demonstrated how a hand method, depending on the skill of the conservator, could be successfully used to repair damaged artwork quickly without requiring expensive equipment. Because the entire sheet does not require complete wetting, artifacts with media too vulnerable for immersion casting can be safely treated with hand technique. Also, more control may be achieved with hand placement of fibers than with mechanical leaf casting. Damaged paper with small-to medium-sized holes are perfect candidates for this method, though larger losses in smooth regular papers are difficult to fill evenly by hand. A combination of hand and mechanical methods for use on a vacuum suction table provides a practical alternative to such problems.
3 VACUUM TABLE
WHEN MARILYN WEIDNER introduced the vacuum suction table at the 1974 AIC meeting, it was difficult to imagine all of its possible applications. Since that time, it has become such an important tool in most laboratories that paper conservators often wonder how they could practice without it. Many people have built, modified, analyzed and used suction tables over the last eight years. Inexpensive home-made models can serve quite well, as can the more expensive and elaborate commercially available models. Important factors to consider for both general use of the vacuum table and leaf casting are:
- Openness of surface. Thick masonry tops tend to restrict air flow and become clogged.
- Flatness of surface. Any material other than very fine screen or some perforated metals will impose their texture on the paper or blotter in contact with it.
- Suction. The pump/fan arrangement should have the capability of lifting a column of water at least 80 inches high.
- Air flow. This will vary depending on the size of the table. Generally 20 cubic feet per minute (CFM) per square foot of table surface is a reasonable guideline. A table 2′ � 3′ (6 � 20 CFM) would perform quite well for most purposes with a suction system that could deliver 120 CFM.
4 LEAF CASTING ON THE SUCTION TABLE
UNTIL RECENTLY, the suction table has been primarily used for washing, drying, stain removal, and lining operations. With only slight modification, the suction table can also be used for localized leaf casting. While hand pulp method remains the simplest and most direct approach for small holes, leaf casting on the suction table may be specially useful under certain conditions:
- In the absence of a conventional leaf casting apparatus.
- When the art object or document is larger than the dimensions of the leaf casting machine.
- When the loss is large and requires a particularly even fill.
- When the texture of the original sheet is an aesthetically important element and the repair calls for articulation of paper texture.
4.1 Advantages of suction table casting
- The entire sheet does not always have to be wet before casting.
- When water-sensitive media are present, another liquid such as alcohol may be utilized to carry the pulp into place.
- Pulp deposition on the original paper is avoided, since very little liquid is used and only a small area of the original is exposed.
- The quality of the join can be improved in cases where strength is important by casting half the fill and then turning the sheet over to complete the fill. This creates an actual encasement or overlapping of the edge on both sides. This variation is not only strong but offers the additional advantage of obscuring a dirty edge.
4.2 Modification of Suction Table for Leaf Casting
With only slight modification, many vacuum/suction table designs may be used for leaf casting. A major issue is the ability of the system to handle safely a gallon or more of water at one time. The liquid should be disposed of before it reaches the suction device. This can be accomplished in several ways:
- Installation of a tee in the tubing leading to the pump/fan. The pipe fitting should be placed so that liquid will fall into a trap for collection and future disposal (see figure 1). Plastic (PVC) tubing and fittings are especially useful for the plumbing. The pipe can be easily cut to size with a handsaw and simply slip-fitted for connection. Though joins can be welded with solvent for permanent high pressure usage, this is not recommended. It is an advantage to be able to undo a connection for later adjustment or alteration.
- Water collection in the plenum space below the table surface. If this space is large enough and waterproof, it can serve as a trap. Vacuum input must be placed high with a removable plug positioned at a low point for water removal (see figure 2).
Fig. 1.
Tee-joint water trap for the suction table.
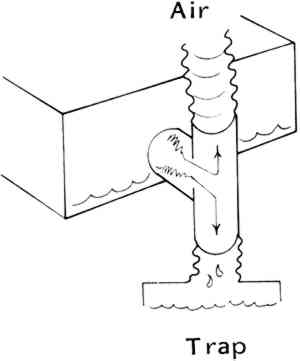 |
Fig. 2.
Plenum space used as a water trap and fitted with a drain.
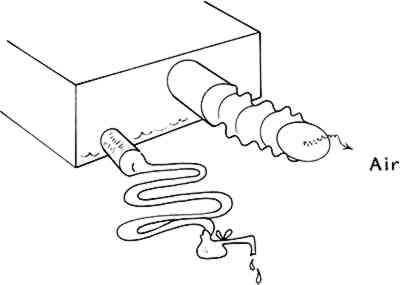 |
4.3 The Process
Leaf casting on the suction table does not differ in principle from the conventional method except that the casting fluid is contained only in the area directly above the loss. A discussion of the process follows:
- The pulp container (see figure 3). Round plastic tubing can be procured in various sizes (2″ to 6″ in diameter) and easily cut into 4″ lengths [1]. (Containers for larger losses are easily fashioned by heating and bending plexiglas sheeting into a rectangular shape, slightly larger than the hole). Thin plastic film (.002″) is cut into a rectangular shape several inches larger than the diameter of the tubing [2]. Then a hole, larger than the loss but slightly smaller than the opening of the container tube, is cut in the center of the rectangle [3]. Silicon adhesive applied to the bottom edge of the tube affixes the container to the plastic mask [4]. This pulp mold will seal itself when suction is applied without harmful downward pressure of the mold on the paper artifact.
- Arrangement of materials on the suction table (see figure 4). A piece of thin plastic film cut larger than the top of the suction table is placed on the surface so that the extending edges hang over the table [1]. A hole in this film is cut centrally, its dimension slightly larger than the opening of the container mask. Two layers of non-woven spunbonded polyester fabric (Reemay, number 2014 or 2114, from Dupont) are placed over the opening to provide a surface on which to cast [2]. Reemay, an especially suitable material, aids in creating very even pulp formation and imparts a texture much like that achieved by contact with papermaker's felts. The damaged original is set on the Reemay so that the loss is located over the opening in the table [3]. The container can be set directly on the surface of the paper [4]. However, the opening in the mask will not conform exactly to the contour of the loss. If precision in casting is required, pulp deposition in areas other than the hole can be avoided by cutting and properly placing a Reemay mask onto the paper [5]. This extra step can be done quickly and enables one to use just a few different-sized containers for most castings.
- Delaying drainage. An interval of time is needed for filling the container with water and pulp. A removable plug can be fashioned using plastic film, cut so that it just fits in the container tube (see figure 4 [6]). A string or narrow strip of plastic affixed to one edge of the plug facilitates removal. The plug, inserted inside the container just prior to applying suction, is pulled tightly against the container mask forming a temporary bottom to the container when suction is activated. Lifting the attached string removes the plug, allowing the slurry to be pulled into the area of loss. Larger areas of loss are plugged better if several pieces of plastic film (each with a tail) are placed to overlap each other slightly. Multiple plug removal becomes a louvre action, thus avoiding tidal waves.
- Selection and processing of pulp. The quality of a casting and its adhesion to the artifact is dependent on many factors: the type of fiber, the nature and duration of processing, and the method of casting and drying. Pulp selection and beating is a complicated issue. The Petherbridge article noted in the bibliography provides a good starting point. However, experimentation and experience is invaluable here. In some cases, it is possible to obtain very satisfactory results by using pulp derived from old, good quality papers beaten in a household blender. The use or addition of linters or commercially processed pulps can provide special advantages in terms of bonding strength and textural quality.
- Correct addition of pulp to casting liquid. Too much pulp yields a fat, irregular, uneven casting and too little will produce transparency and thinness. (As previously mentioned, it may be desirable in some cases to cast a thin fill from one side, turn the paper over, and complete the casting from the other side. This encases the edge of the original, providing more strength at the join, while perhaps hiding a dirty edge.) The achievement of a fill that has comparable thickness to the original as well as appropriate texture and opacity is a complicated matter, and practicing on holes in mock-ups is necessary to master this technique. However, it is helpful to have a starting point, and the following indicates a method:5,6Cast, press, dry, and cut a rectangle of paper to a convenient size (e.g., 20cm � 25cm). Measure and record the thickness and weight of the sample (e.g., .0125cm thick and 4.0 grams).Determine volume-per-gram by multiplying the length of rectangle times the width times the thickness and divide by the weight of sample (e.g., 20cm � 25cm � .0125cm divided by 4 grams = 1.563 cm3/gram).Find the area of the loss and measure the thickness of the damaged artifact. Counting squares of graph paper or outlining the perimeter of the hole with a planimeter are two methods that have been used to approximate area. Either technique is adequate for occasional casting. However, if the volume of leaf casting activity is high, it may be worth speeding area calculation with the aid of a microcomputer. Simply tracing the outline of the loss with a “light pen” on a Graphics Tablet connected to an Apple Computer, for example, will yield a very quick and accurate area measurement.Determine the weight of pulp required for the casting by dividing the volume of the loss by the volume of a gram of pulp (e.g., area of loss 150cm22 � thickness of artifact .017cm divided by volume/gram 1.563cm33 = 1.63 grams).It is convenient to refrigerate pulp in solutions of known concentration (e.g., 1%) for storage. It is then easy to mix different colored pulps, test the resulting color by drying, and pour out the required amount (e.g., 1.63 grams is approximately equal to 163ml of a 1% solution). The addition of a small quantity of fungicide to the solution will prevent bacterial and mould growth.
- With suction holding the container and plug in position, the pulp solution is poured into the container. Vacuum pressure is then adjusted. This is a matter of experience, but pressure influences flow and the flow rate will affect the casting. The tail of the plug is quickly pulled. This action opens the bottom of the container, enabling the liquid to drain.
- The casting is quite wet and much water can be removed by slipping a sheet of blotting paper between the first and second layers of Reemay. Acting as a support, the Reemay can then be lifted to move the paper to a hard-surfaced table. Rubbing over the fill with a bone burnisher while it is still wet serves to compact fibers and improve the join. Using plastic film or polyester fabric as an interleaf during burnishing will help to achieve a more sympathetic match of textural qualities. Subsequent drying of the sheet in open air is often preferable to pressing even under light weight. Remoistening for final pressing and flattening is accomplished with controlled, even water application. By this time, the joined areas are more secure and not as susceptible to splitting.Large castings have a tendency to detach at the join, a condition that is exacerbated when the artifact is particularly expansive. Pressing or slowing the drying process may be necessary to maintain the integrity of the bond.Very tender attachments or those that will have to withstand the strain of handling, can be strengthened with application of Japanese tissue along the join or all over as a lining.3
- If the addition of adhesives to the fill seems appropriate—for strength or as a sizing for later toning—then it might either be added to the casting solution or applied locally after the fill has undergone preliminary air drying.
- In special cases, it is desirable to approximate the textural qualities of the original in the casting. Articulation of laid lines in the cast area can minimize the visibility of damage. This becomes important with a work of art on textured paper scheduled for exhibition in subdued and slightly raking light. The use of a laid screen, aligned on a light table to match the laid markings of the paper and placed just under the loss during the casting process, can impart a sympathetic texture to the fill. A method for creating an assortment of laid screens for this purpose is described as follows:Make a ruled line drawing using black ink on clear acetate. The width of the lines should be drawn to equal the space in between the lines. Lay out the grid so that approximately 24 black lines are set to the inch (see figure 5).Using a photostat machine, incrementally enlarge and reduce the line drawing to achieve a desired range of sizes.Place a line drawing in direct contact with a piece of photo-silk screen emulsion. The photo-sensitive emulsion is a commercially available product mounted on a plastic film support. One company that supplies this material is J. Ulano & Company, 610 Dean St., Brooklyn, N.Y. 11238.Set a sheet of glass on top of the sandwich and expose the emulsion to light through the open areas of the line drawing. A 250 watt sun lamp is a good source and it will work well if placed 15–20 inches from the drawing. Exposure will probably be under 12 minutes but a little testing is required to achieve the proper duration (dwell time).After exposure, place the emulsion into a liquid developer specific for this purpose. Rinse according to the emulsion directions and while the emulsion is wet and sticky, press it onto a support of Reemay or fine (polyester) silk-screen fabric. Allow to dry and then remove the plastic film carrier.The dried emulsion remains sensitive to water and must be hardened before use. Expose the silk screen to the fumes generated by a formaldehyde bath and allow to dry. Then spray the screen with a material such as Scotchgard to protect the emulsion further.Repeat this process for each line drawing to create a catalog of various-sized screens that can be used again and again.It should be noted that this process is not for the creation of a perfect reproduction or a facsimile of a missing area. Instead, its use is intended to minimize the visibility of damage that would otherwise interfere with the aesthetic impact of a work of art.
- Casting with alcohol. There are instances where even partial wetting of a paper artifact is not safe. Experiments have shown that an acceptable casting can still be accomplished, providing the paper or media are not adversely affected by alcohol. The pulp is prepared by first beating it in water in the usual manner. Most of the water used in beating is extracted by pouring the slurry through a strainer. The damp fibers are transferred back to the blender where a quantity of ethanol is added for a second beating. The paper artifact is wet with ethanol prior to placement on the table and casting is performed as previously described. The resulting fill will be quite soft and felt-like because not much bonding occurs. However, this may be remedied by localized application of water or water plus a sizing agent followed by burnishing and pressing.
Fig. 3.
Pulp container for use on the suction table.
 |
Fig. 4.
Suction table set up with damaged object, pulp container, and associated materials, ready for use.
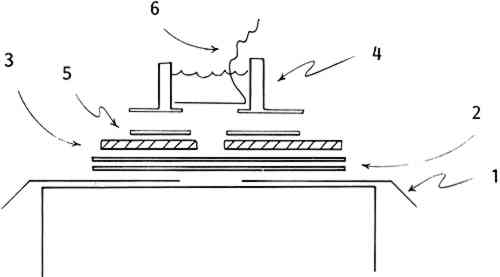 |
Fig. 5.
Suitable line spacing to make a laid-line pattern in casting.
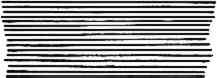 |
5 ALTERATION OF THE VACUUM TABLE DESIGN
RECENTLY we constructed a small portable vacuum table that especially lends itself to leaf casting and pulp filling procedures. It is made entirely of clear plastic, so that when it is placed on a light table, light is transmitted up through the top of the suction box. Permeability of a small part of the upper surface was achieved by drilling many tiny holes in the Plexiglas. Marjorie Cohn suggested at the Milwaukee meeting that a fritted glass plate might be set in the top surface to allow transmission of light without the need for drilling. A full size transparent suction table would be most desirable. Recently, T. K. McKlintoc proposed the use of etched syntered polyethylene as a surface. This translucent porous material, supported by plastic lighting difuser, would result in a device that could serve both leaf casting and conventional suction table needs alike. An illustration of a possible design is shown below (figure 6).
Fig. 6.
A light-transmitting suction table for pulp casting or treatment of a small area.
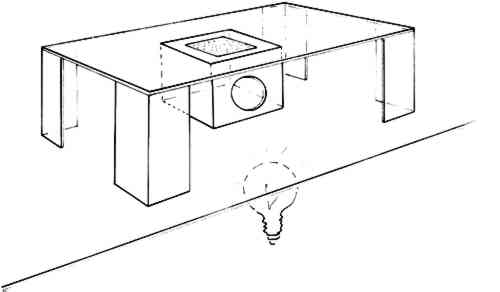 |
5.1 Working features of a transmitting suction table
- A light suction table is extremely versatile. It can serve for leaf casting as just described, conventional pulp filling, and for very precise and selective addition and deposition of pulp.
- For conventional pulp filling, suction is applied but temporarily blocked by placement of a sheet of thin plastic film over the opening of the table. When proper pulp density and distribution is achieved, the “table cloth” (plastic film) is yanked and the liquid quickly falls, leaving the fibers in place.
- For certain shaped holes or art that cannot tolerate much wetting, a transmitting table is extremely useful. A dirty edge or a small loss, tear or paper thinning is set on Reemay over the suction area with the vacuum on. Pulp, suspended in very dilute concentration, is dripped onto the damaged area with a wide-tipped medicine dropper. Air flow takes the pulp to the open area and causes adhesion to the edge of the top or to the previously dripped application. It is possible to build up multiple layers until the desired result is achieved without much lateral wetting. It is necessary to send distinct droplets. Attempting pulp application from close range will result in fiber clumping.
6 CONCLUSION
THE LEAF CASTING TECHNIQUE offers a quick and viable alternative to traditional repair techniques. Conducting this kind of procedure on a common suction table increases both the number of artifacts that can be treated and the number of laboratories capable of doing the work. The use of transparent suction tables and silk-screens designed to impart texture to the castings provide further refinement now available to the conservator.
ACKNOWLEDGEMENTS
THE SUCCESS of this project was dependent on the help and patience of all the people in our laboratory, namely Pauline Mohr, Patricia Morris, Linda Odgen, Sylvia Rodgers, and Janice Mae Schopfer. Special acknowledgement goes to Keiko Keyes. It was through several meetings with Keiko that the original concept was refined and simplified. Finally, this paper became much more readable after the careful attention of Jennifer Futernick.
REFERENCES
Alkalaj, Stella. “The Chemical Laboratory for Hygiene, Conservation and Restoration of Damaged Written Materials.” Restaurator1:2 (1969), pp.87–91.
Wachter, Otto: “Methods of Restoring Old Prints, Documents and Drawings Using Liquid Paper Pulp,” I.I.C. Lisbon Conference 1972, Conservation of Paintings and the Graphics Arts (1972), pp. 971–974.
Alkalay, Esther Boyd. “The History and Development of Leaf Casting,” The Conservation of Library and Archive Materials and the Graphics Arts, Cambridge 1980 Preprints (1980), p. 187.
Petherbridge, Guy. “Analysis, Specification, and Calculation in the Preparation of Leaf Casting Pulp: A Methodology.” The Conservation of Library and Archive Material and the Graphic Arts, Cambridge 1980 Preprints (1980), pp. 189–209.
Keyes, Keiko Mizushima, and Farnsworth, Donald S. “Practical Application of Paper Pulp in the Conservation of Works of Art on Paper.” Preprints. Fourth annual meeting of the American Institute for Conservation (1976), pp. 76–86.
Perkinson, Roy, and Futernick, Robert. “Questions Concerning the Design of Paper Pulp for Repairing Art on Paper.” Preservation of Paper and Textiles of Historic and Artistic Value. No. 164, 1977 (JohnWilliam, editor; published by American Chemical Society).
Weidner, Marilyn Kemp. “A Vacuum Table of Use in Paper Conservation.” Bulletin of the American Institute for Conservation14:2 (1974).
DuMeer, Robert, “Construction of a Leaf Caster for Small Laboratories.” Preprints. Sixth annual meeting of the American Institute for Conservation, 1978.
Section Index |