THE EFFECT OF AN ALKALINE RINSE ON THE AGING OF CELLULOSIC TEXTILES, PARTS I AND II
Ira Block
ABSTRACT—In Part I of a four-part series, the author reviews the literature on the aging of cellulose, notes the reasons why an alkaline rinse should be effective in retarding the aging of cellulosic textiles, and presents preliminary results which indicate that treating new cotton and rayon cloth with a dilute calcium hydroxide solution can increase their resistance to accelerated aging.In Part II the results of a more detailed study of the effect of a calcium hydroxide rinse on the strength retention and color change of new cellulosic fabrics are reported. It is shown that the treatment is successful in retarding strength loss, but that it has no effect upon color change.
1 PART I: PRELIMINARY RESULTS
1.1 INTRODUCTION
DURING A SABBATICAL YEAR tenure at the Conservation Analytical Laboratory of the-Smithsonian Institution, the author studied the efficacy of the deacidification of cellulosic textile materials as a conservation treatment. In this series of papers the some-what unexpected results of this investigation are reported. In Part I, the reasons for believing that deacidification would be effective are discussed, and preliminary results on new rayon and cotton cloth are presented. Part II reports a detailed examination of the kinetics of strength loss and color change.
Part III will report the effect of a calcium hydroxide rinse on artifically aged cellulosics, which turns out to be less effective than on new cloth. This leads to the prediction that an alkaline rinse will not be more effective than soaking in deionized water when treating old cellulosic fabrics. Part IV shows that the conclusions reached in Part III are valid and explains why. It is shown that provision of an alkaline reserve is effective in retarding the degradation of new fabrics, but is useful for old fabrics only in protecting against the absorption of acidic species from the environment.
In a recent review article, Daniels1 pointed out that as early as 1898 it was known that the acidic impurities in paper could greatly increase its rate of deterioration. Shaw and O'Leary2 noted in their investigations on the stability of book papers that “calcium carbonate pigments had a protective or inhibiting effect in the aging test,” and Barrow's3 investigation of the causes of deterioration of books showed that treatment with an alkaline solution could increase the life of books by neutralizing the acids present in the paper and by providing an alkaline reservoir which would shield against further acidification.
Although it is well known that washing or rinsing old paper in clean, pure water can improve its color, strength and folding endurance, it has been only recently that the alkaline treatment of nearly neutral papers has been investigated. Tang and Jones4 noted that “Distilled or deionized water passed through a column of calcium carbonate chips becomes acceptable for paper washing, and can be used without shortening the life of the paper.” Wilson, et al5 have discussed the efficacy of magnesium bicarbonate treatment of old papers, and other workers have investigated the protection afforded paper when rinsed with amines6, 7 and organometallic compounds.8, 9
The above work is of some significance to the conservation of textile products, since cellulosic fibers such as cotton, linen, jute and rayon comprise an appreciable fraction of textile artifacts. These materials are often washed as part of their conservation treatment, and the usual procedure for the care of textiles,10–15 as was once the case for the treatment of paper,16 has been to use water of as high a quality as possible. However, if when washing is indicated, a mildly alkaline rinse could enhance the resistance of cellulosic textile fibers to degradation at ambient temperatures, conservators would be provided with an important new tool for treating many fabrics.
The literature indicates that it should be possible to stabilize cellulosic textiles, for which washing is indicated as part of the conservation treatment, by a mild alkaline rinse which would neutralize the internal acids. This procedure appears to have been originally recommended by Pahir in a 1925 patent and rediscovered by Wilkie in 1929.17
In addition to the literature on paper conservation, other work leads to this conclusion. Peters and Still18 point out that it “is difficult to differentiate the thermal degradation at low temperatures from the normal aging of cellulose.” They note that the degradation of cotton is greater in air than in nitrogen and is enhanced by moisture, and suggest that the formation of carboxyl (− COOH) and carbonyl (>C = 0) groups is important in the degradation of cellulose. Arney, et al19, 20 argue that the degradation of cellulose in paper is due to both oxygen-dependent and oxygen-independent processes, and that both types of processes are affected by deacidification treatments. They further state that their results suggest that “the influence of acidity on the rate of natural paper degradation would be the same regardless of which degradation process predominates at room temperature.”
In a series of investigations, Davidson and Nevelle21 studied the degradation of acidic oxycelluloses. They were able to show that a major cause of the degradation of cellulose is the formation of carboxyl groups on the C6 carbon of the anhydroglucose unit. Davidson and Standing22 hypothesized that “hydrolysis of the glycosidic linkages is catalysed by hydrogen ions derived from the ionization of the free (unneutralized) carboxyl groups in the oxycellulose molecule.” It was shown that oxycelluloses containing the free acid were unstable even when stored at room temperature and low relative humidities, and that conversion of the carboxyl groups from the free acid to the sodium salt form greatly stabilized the cellulose.23 More recent studies by Shenai and Shah24 among others, supported these conclusions.
1.2 EXPERIMENTAL
THE ACCELERATED AGING of fibrous materials by oxidation in both dry and humid ovens at various temperatures, with and without light, has been intensively studied.25–38 Since artificially degraded fabrics do not duplicate naturally aged materials in all respects (cf reference 39), it is necessary to choose a test protocol in which the chemical processes do not differ substantially from those occurring at room temperature, yet proceed rapidly enough to allow results to be obtained in a reasonable time period. As noted earlier,18 low temperature thermal degradation is almost identical to normal aging. The problem is to determine how high a temperature can be considered “low”.
Wilson and Parks25 noted that artificial aging at 100�C “with some moisture” gave results that were closer to naturally aged paper than did artificial aging at 90�C and 50% R.H. Unfortunately, cellulosic textiles do not age rapidly enough at 100�C to permit a reasonable time frame for the experiment. In this work it was found that dry baking at 100�C for one week caused essentially no change in fabric properties, in agreement with the data of Kerr, et al.40 However, a review of the literature25–38 indicates that temperatures below 180�C do not introduce chemical reactions which are not present at room temperature. It was, therefore, decided to conduct the aging at 150�C at low humidity.
It should be noted that at this writing the only accepted standards for aging of textile materials are those promulgated by the American Association of Textile Chemists and Colorists (AATCC). These tests, AATCC 26-1978 and 111A,B,C,D-1978, are specifically devised for determining the resistance of textiles to sulfur dyes and weather resistance, respectively, and are not applicable to comparisons of the relative effectiveness of methods for reducing the rate of degradation of fabrics. Thus, the author has endeavored to apply a test method which would not introduce extraneous chemical reactions and which would permit comparisons between treatments. Although it is recognized that other environmental factors such as light, relative humidity and atmospheric gases will affect the results of both natural and accelerated aging, it was decided to limit this study of the effect of elevated temperature and low humidity. In this way, different treatments can be compared with a minimum of extraneous factors, while still taking into account the important role played by moisture.
1.2.1 Fabric
The fabrics in this study were a plain weave, 80 � 80 cotton print cloth weighing 103 g/sq m (no. 400) and a plain weave, 80 � 80 spun rayon cloth weighing 132 g/sq m (no. 266) supplied by Testfabrics Inc. The cloths were washed and dried twice as per AATCC Test Method No. 124-1978.
1.2.2 Reagents
The reagents used were calcium hydroxide [Ca(OH)2] and sodium carbonate [Na2CO3] supplied by Fisher Scientific Co., and deionized water of about 1 megohm resistance.
Calcium hydroxide solution was prepared by adding at least three grams of solid to one liter of water, shaking and allowing the solids to settle overnight. Fifty milliliters of the saturated solution were made up to one liter to provide an approximately 0.01% (w/v) solution with a pH of 9–9.5.
A saturated solution of sodium carbonate was prepared in a similar manner, and 1.4 ml were made up to one liter to give an approximately 0.01% (w/v) solution.
1.2.3 Application
The test fabrics were cut to the proper dimensions with an NAEF die. Nine of the specimens were added to a one-liter bath of solution maintained at 30�C by circulation of the solution through a coil of polyethylene tubing immersed in a temperature-controlled bath. Solution pH was maintained by dropwise addition of the saturated solution [(Ca(OH)2 or Na2CO3 as appropriate] to the rinse bath.
For treatment A, the specimens were soaked for 2 hr in Ca(OH)2 solution maintained at a pH between 9.0 and 9.5, removed from the bath, and soaked an additional hour in the Na2CO3 solution at 30�C to precipitate CaCO3,19 drained and dried overnight on glass fiber screens.
For treatment B, specimens were soaked for 3 hr in Ca(OH)2, removed from the bath, given a fast rinse in deionized water to remove surface solution, drained and dried overnight on glass fiber screens. The Ca(OH)2 converts to CaCO3 by reaction with the carbon dioxide in the atmosphere.
1.2.4 Aging
Each sample was made up of three specimens of fabric chosen at random from the treated or untreated materials as applicable. Each of the specimens in a sample was supported on a glass fiber screen while being baked in a Fisher Isotemp forced draft oven at 150 � 2�C. Since the oven was open to the atmosphere in the laboratory (approx. 21�C and 55% RH) the relative humidity in the oven varied, but remained low, in keeping with the recommendation of Wilson and Parks25 and the work of Williams, et al.27
Upon removal from the oven after baking, samples were stored in a closed container over silica gel until cool. After cooling samples were stored in sealed plastic bags until testing.
1.2.5 Tear Testing
Prior to testing, the bags containing the samples were opened and the samples were stored at standard conditions of 21�C and 65% RH for at least twelve hours.
The degradation of the samples was measured by the loss in tear strength. This parameter was chosen since, as the work of Berry, et al.39 shows, both tear strength and tensile strength follow essentially the same kinetics; tear testing is more rapidly performed than tensile testing; and tearing more closely approximates the stresses put on a fabric when handled than does tensile testing. Tear testing was performed on an Elmendorf Apparatus as per ASTM D 1424–63, at 21% and 65% RH.
1.3 RESULTS AND DISCUSSION
IN A SERIES OF preliminary experiments it was found that soaking in Ca(OH)2 solution for 2 hours gave the same weight gain as soaking for five hours. Thus, the 2-hr or the 3-hr soak provided the maximum uptake of calcium, about 2% calcium carbonate on weight of fabric (owf). The surface pH of the samples was measured with an lonalyzer fitted with a flat-bottomed electrode. It was found that the untreated fabric samples had a pH of 5.5 to 6.0, that the pH of samples immediately after soaking was between 8.0 and 8.5, and that the pH fell to between 7.0 and 7.5 after drying overnight.
Tear strength and color of the treated samples was measured and found to be essentially the same as the control fabric. Subjective evaluation of the hand indicated that the treatments did not cause harshening or brittleness.
The major results of this portion of the study are shown in Fig. 1. The logarithm of the percent strength retained is plotted versus the logarithm of the baking time. This corresponds to an equation of the form
Fig. .
 |
and would, if tear strength were related directly to the chemistry of the system, relate directly to the reaction rates. It should be noted, however, that tear strength is a complex function of fabric and yarn structure as well as fiber strength, so that the results should not be interpreted as a quantitative description of the chemistry of the system. For as Arney, et al.19 have noted “the influence of acidity on the thermally induced deterioration of [cellulosics] appears to be more complex than has previously been assumed, and the way in which deacidification treatments may alter the various deterioration processes is, as yet, not thoroughly understood.”
Fig. 1.
Logarithm of Percent Strength Retained vs Logarithm of Baking Time.
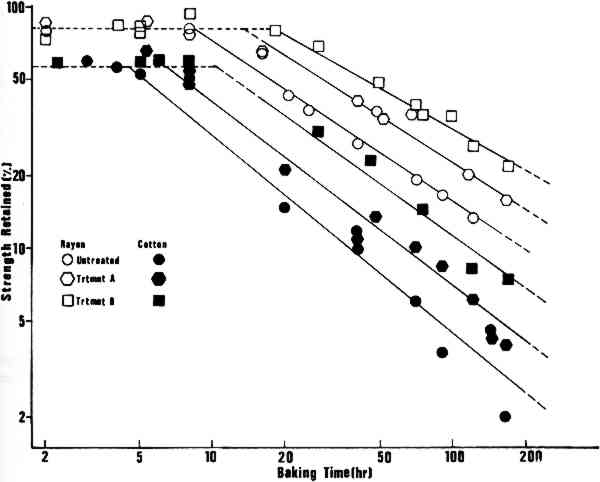 |
The curves of Fig. 1 reveal three important features: (1) an initial period in which log(Strength Retained), (Y), is insensitive to the log(Baking Time), (T), (2) a later period in which Y decreases linearly with T, and (3) the point at which Y becomes sensitive to T.
Since the early data for both treated and untreated fabrics fall on a single line with zero slope, we may conclude that identical processes are at work in the cotton samples irrespective of treatment, and that the rayon samples are subject to the same processes irrespective of treatment. However, the chemistry of the rayon system may be different from that of the cotton.
At some point, Y begins to decrease linearly with T. The slopes of the lines are:
Regression analysis indicates that there is no significant difference between the slopes of the three lines for each of the respective fibers. Thus we may, again, conclude that identical processes are operating in the cotton samples irrespective of treatment, and that the same holds true for the rayon cloth.
The time at which the alkaline treatment begins to lose its efficacy, (Tc), is found to be about 4.5 hr for the untreated cotton, about 7 hr for the samples subjected to Treatment A and about 10 hr for the samples which were given Treatment B. For the rayon samples, these events occur at about 8 hr, 12 hr and 19 hr, respectively. It is interesting to note that in both cases the ratio of Tc for Treatment A to Tc for the control is about 1.5 and the ratio of Tc for Treatment B to Tc for the control is about 2.5. This equivalence indicates that the treatment is effective irrespective of the source of the cellulose, and may mean that the chemistry of the degradation process is independent of the source of the cellulose.
Treatment A is not as effective as Treatment B, probably because rinsing did not remove all of the sodium ions. Clapp has pointed out the deleterious effects of sodium on the aging of paper.16 To test this hypothesis a set of samples was subjected to Treatment A, but given only a fast rinse in deionized water. The treated samples degraded faster than the controls.
We may postulate, then, that the effect of the calcium carbonate is to inhibit the deterioration processes, and that at some point the calcium ions are no longer effective. It is at this point that the slope of Y vs T abruptly changes.
1.4 CONCLUSIONS
FROM THE RESULTS to date, it appears that soaking new cotton or rayon cloth for about 3 hours in a 0.01% calcium hydroxide bath at 30�C and allowing it to air dry can increase its lifetime by about a factor of 2.5 without affecting color or hand.
2 PART II: STRENGTH RETENTION AND COLOR CHANGE
2.1 INTRODUCTION
IN PART I, it was reported that a treatment in dilute calcium hydroxide solution could increase the resistance of cellulosic textiles to degradation by heating at 150�C, an accelerated aging test that should predict the results of natural aging. It was found that the logarithm of the percent strength retained (Y) could be related to the logarithm of the baking time (T) by an equation of the form: Y = A + n�T. The slopes of the lines for specimens which remained untreated or were subject to treatment for each of the respective fibers were essentially the same, and it was concluded that the treatment is effective irrespective of the source of the cellulose. In addition, it appeared that the chemistry of the degradation process was independent of the source of the cellulose.
This part presents the results of a more detailed study of the effect of a Ca(OH)2 rinse on the strength retention and color change of new cellulosic fabrics subjected to accelerated aging.
2.2 EXPERIMENTAL
2.2.1 Color Measurement
The color change of the test samples was monitored by measuring the color of fabric samples with a Hunterlab Model D25D2 Color/Difference Meter. A glossy black support was used to insure that the background color for all measurements was the same. The details of reagent application, aging and tear testing were provided in Part I.
2.3 RESULTS
2.3.1 Strength Retention
The results of this study of the strength retention of artificially aged cotton and spun rayon fabric are shown in Figs. 2 and 3, respectively. If first-order kinetics apply, the rate of decrease in strength retention should be proportional to the strength retained, and a plot of the log(strength retained) vs time would be linear. In both cases, it is seen that such an assumption is valid for less than forty hours baking time at 150�C
Fig. 2.
Strength Retained vs. Baking Time at 150�C for Cotton Cloth.
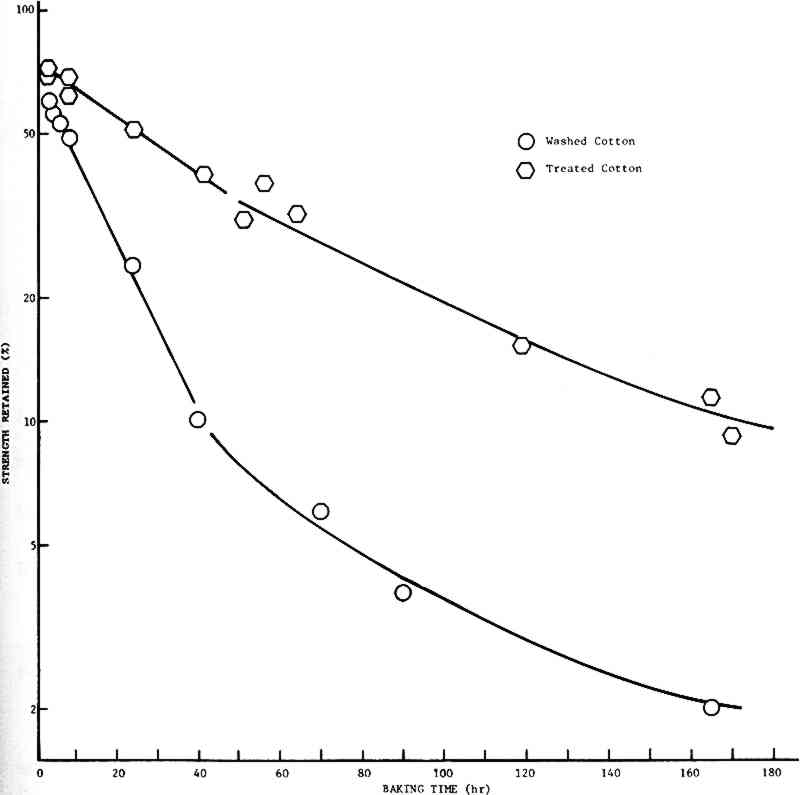 |
Fig. 3.
Strength Retained vs. Baking Time at 150�C for Rayon Cloth.
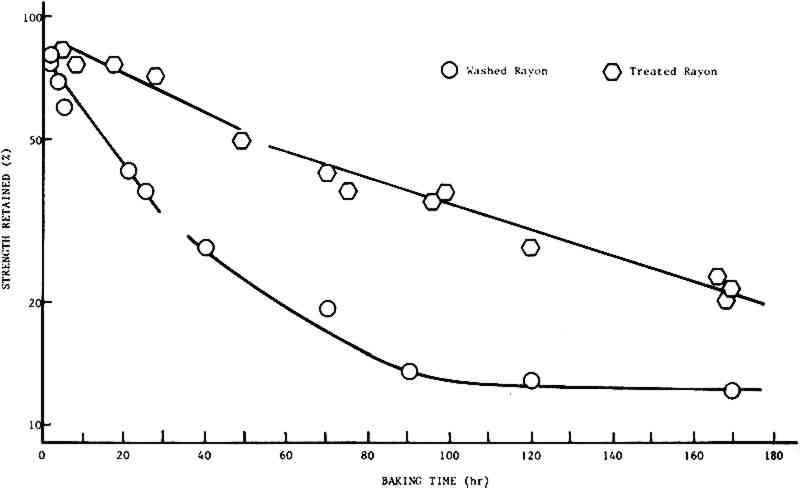 |
Beyond forty hours the curves for the untreated material exhibit definite concavity. The treated material, however, continues to follow first-order (or psuedo first-order) kinetics to about 120 hr. The rate of strength loss for the treated materials, as measured by the initial slopes of the lines, are found to be about one-half that of the untreated materials. For cotton, the untreated fabric degrades at a rate of about 1.8%/hr, while the treated cloth degrades at a rate of only 0.9%/hr. The untreated rayon cloth loses strength at the rate of about 1.7%/hr, while the treated cloth degrades at only about 0.7%/hr. In addition, the decay rates are essentially the same for both cotton and rayon.
It should be noted that, since the parameter being measured is a physical property that is only indirectly related to the chemistry of the cellulose polymer making up the fibers, the more curves depart from linearity, the less meaningful comparisons between them become. Thus, comparisons of the rates of decay of treated and untreated cloths for times greater than forty hours should be limited to the observation that the treated fabrics degrade at a lesser rate than the untreated fabrics. However, it is of interest to note that the decay rates for both the treated cotton and treated rayon cloths are almost identical (about 0.2%/hr). This is in keeping with the observation in Part I that the rates of decay appear to be independent of the source of the cellulose.
Finally, it may be seen that there is a very rapid strength loss occurring in the first hour or so of baking. This phenomenon is not unexpected, since the fabrics contain some moisture when placed in the oven, and it has been demonstrated in Part I (and see refs. 25, 27, 29, 36–38, 40) that moisture accelerates the rate of degradation.
2.3.2 Color Change
The assumption that the change in color of the fabrics would be affected only by some chemical species in the cellulose and oxygen allows us to write:
Fig. .
 |
where E is the color, [O] the concentration of oxygen at the surface of the fabric, and [C] the concentration of the cellulose moiety that causes the color change.
If [C] remains constant, then (because [O] is constant), we may write
Fig. .
 |
where Et is the color at time ‘t’, and Eo is the original color. The change in color should be linear with time. It was found, however, that the rate of color change did not remain linear with time, but decreased as the fabric became darker. This phenomenon comes about because the color meter cannot detect small differences between large color changes. In order to avoid this problem, we may define the following parameter:
Fig. .
 |
where Ef = the color at infinitely long baking times, Et = the color at time ‘t’, and Eo = the original color. Ef was determined by measuring the color of samples baked for over 400 hr. The value of F is ‘1’ if there is no color change, and ‘0’ when the maximum has been reached. Thus, a plot of (1 – F) vs time should be linear.
Figure 4 shows the plots of (1 – F) vs time for treated and untreated cotton and rayon. Of major interest is the fact that there is no apparent difference in the rate of color change for treated and untreated cloth. That the yellowing and darkening of cellulosic material is not affected by an alkaline treatment indicates that the species which cause the change in color are not acids. This result is in agreement with those of Albeck, et al41 who concluded that “the yellowing tendency of [oxidized] cottons is found to depend solely on the aldehyde groups content, the ketone and carboxyl groups having no appreciable influence.”
Fig. 4.
Normalized Color Change vs. Baking Time at 150�C for Cotton and Rayon Cloths.
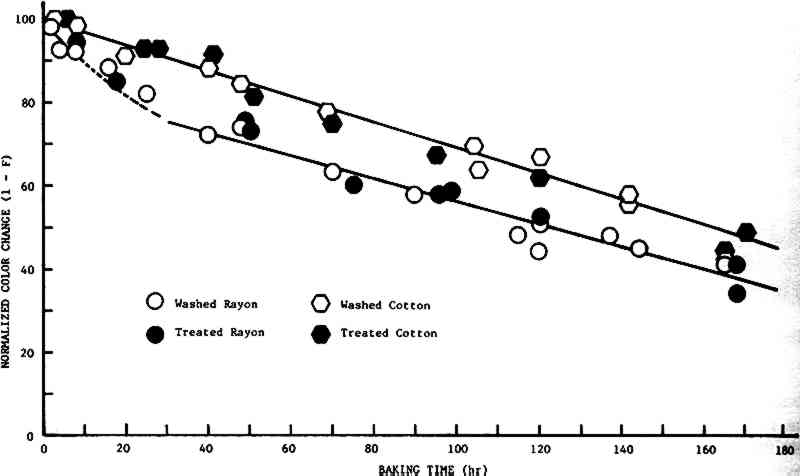 |
Furthermore, we see that the initial rate of discoloration of the rayon is greater than that of cotton, while at times greater than 40 hr it is the same (about 0.3 units/hr). This effect may be due to the higher surface area of the finer rayon fibers compared to the cotton. Increased surface area would permit a more rapid diffusion of moisture from the fiber, which might enhance the rate of reaction at the air/fiber interface if, as is likely, moisture influences the reaction rate. It should be noted that the result could also be ascribed to the fact that the cotton has a dense cuticle layer which the rayon lacks, so that these phenomena may be due to a combination of surface area and cuticle.
2.4 CONCLUSIONS
FROM THE RESULTS of this work to date, it may be concluded that rinsing new cellulosic textiles in a dilute calcium hydroxide solution enhances resistance to strength loss caused by thermal degradation by about a factor of 2, but has little or no effect on the darkening of the fibers, and that these results are independent of the source of the cellulose. In addition, the darkening of cellulosic textiles appears to proceed through the formation of aldehydes rather than acids.
ACKNOWLEDGEMENTS
THE AUTHOR WISHES to thank Mrs. Lucia Tang for her helpful suggestions, and the Conservation Analytical Laboratory of the Smithsonian Institution and the University of Maryland for their support, both financial and moral, of this work.
REFERENCESSummarized descriptions of this research project have appeared in the Preprints of the American Institute for Conservation 1981 Meeting (Philadelphia), pp. 37–45 and of the International Institute for Conservation 1982 Meeting (Washington), pp. 96–99.
Daniels, V., “Aqueous Deacidification of Paper,” The Conservation of Library and Archival Materials and the Graphic Arts, Cambridge, 1980.
Shaw, M.B. and M.J.O'Leary, “Effect of Filling and Sizing Materials on Stability of Book Papers,” National Bureau of Standards Research Journal, 21, 671 (1938).
Barrow, W.J., Permanence/Durability of the Book, Parts 1–7, W.J. Barrow Research Laboratory, Richmond, Va.
Tang, L.C.N.M.M.Jones, “The Effects of Wash Water Quality on the Aging Characteristics of Paper,” J. of the A.I.C., 18, 61 (1979).
Wilson, W.K., R.A.Golding, R.H.McLaren and J.L.Gear, “Changes in Properties of Papers After Treatment with Magnesium Bicarbonate Solution,” Abstracts of the 178th Annual Meeting of the American Chemical Society.
Zeronian, S.H. “Conservation of Textiles Manufactured from Man-Made Fibers,” Advances in Chemistry Series No. 164, 208, American Chemical Society, 1977.
Hofenk-deGraaff, J.H., “The Effects of Chloramine-T on Paper,” Fourth Triennial Meeting of the ICOM Committee for Conservation, Venice, 1975.
Kelly, G.B. and J.C.Williams, “Inhibition of Light Sensitivity in Papers Deacidified with Diethyl Zinc,” Abstracts of the 178th Annual Meeting of the American Chemical Society.
McCarthy, P., “Vapor Phase Deacidification: A New Preservation Method,” The American Archivist, 32(4), 333 (1969).
Landi, S.B., “The Equipment of a Textile Conservation Workroom,” Textile Conservation, J.E.Leene, Ed., 128, I.I.C., 1972.
Reeves, P., “Some Techniques of Textile Conservation Including the Use of a Vacuum Hot Table,” Advances in Chemistry Series No. 164, 181, ACS, 1977.
Finch, K. and G.Putnam, Caring for Textiles, Watson-Guptill Publications, New York, 1977.
Leene, J.E., Ed., Textile Conservation, I.I.C., 1972.
Burnham, M.D., “Cleaning of Archaeological Textiles,” Irene Emery Roundtable, 1974, Textile Museum.
Collins, M., “How to Wet-Clean Undyed Cotton and Linen,” Information Leaflet No. 478, Smithsonian Institution, 1967.
Clapp, A.F., Curatorial Care of Works of Art on Paper, Intermuseum Conservation Association, 1974.
Wilkie, J.B., “Laundry ‘Winter Damage,’ ” National Bureau of Standards Research Journal, 6, 593 (1931).
Peters, R.H. and R.H.Still, “Some Aspects of the Degradation of Polymers Used in Textile Applications,” Applied Fibre Science: II, F.Happey, Ed., 321, Academic Press, New York, 1979.
Arney, J.S., A.J.Jacobs and R.Newman, “The Influence of Deacidification on the Deterioration of Paper,” J. of the A.I.C., 19(1), 34 (1979).
Arney, J.S. and A.H.Chapdelaine, “A Kinetic Study of the Influence of Acidity on the Accelerated Aging of Paper,” Preservation of Paper and Textiles of Historic and Artistic Value II, J.C.Williams, Ed., 189, American Chemical Society, Washington, D.C., 1981.
Davidson, G.F. and T.P.Nevelle, “The Acidic Properties of Cotton Cellulose and Derived Oxycelluloses: Part I–VI,” J. Textile Institute, 39, T59 (1948).
Davidson, G.F. and H.A.Standing, “Auto-Hydrolysis of Acidic Oxycelluloses,” J. Textile Inst., 47, T141 (1951).
Davidson, G.F. and T.P.Nevelle, “The Auto-Hydrolysis of Acidic Oxycelluloses,” J. Textile Inst., 47, T439 (1956).
Shenai, V.A. and K.D.Shah, “Studies in Accelerated Oxidation of Cellulose: Part III,” Textile Research J., 44(3), 214 (1974).
Wilson, W.K. and E.J.Parks, “Comparison of Accelerated Aging of Book Papers in 1937 with Thirty Six Years Natural Aging,” U.S. National Bureau of Standards, IR74–632, 1974.
Wilson, W.K. and E.J.Parks, “An Analysis of the Aging of Paper,” U.S. National Bureau of Standards, IR74–499, 1974.
Williams, J.C., C.S.Fowler, M.S.Lyon and T.L.Merrill, “Metallic Catalysts in the Oxidative Degradation of Paper,” Advances in Chemistry Series No. 164, ACS, 1977.
Zeronian, S.H., “Heat-Induced Changes in Properties of Cotton Fibers, Cellulose Chemistry and Technology,” ACS Symposium Series No. 48, ACS, 1977.
Leene, J.E., L.Demeny, R.J.Elema, A.J.deGraaf and J.J.Surtel, “Artificial Aging of Yarns in Presence as well as in Absence of Light and Under Different Atmospheric Conditions,” Fourth Triennial Meeting of the ICOM Committee for Conservation, Venice, 1975.
Kosik, M., V.Luzakova and V.Reiser, “Study on the Thermal Destruction of Cellulose and its Derivatives,” Cellulose Chemistry and Technology, 6, 589 (1972).
Shenai, V.A. and O.P.Singh, “Studies in Accelerated Oxidation of Cellulose: Part I,” J. Society of Dyers and Colourists, 87(7), 228(1971).
Roffael, E. and K.Schaller, “Effect of Heat Treatment on Cellulose,” Holz. Roh-Werkst., 29(7), 275 (1971).
Grey, C.G., “An Accelerated Aging Study Comparing Kinetic Rates vs TAPPI Standard 453,” Tappi, 52. 325 (1969).
Wilson, W.K. and B.W.Forshee, “Degradation of Cellulose Acetate Films,” Society of Plastics Engineers J., 15, 146 (1959).
Evans, E.F. and L.F.McBurney “Oxidative Stability of Cellulose Derivatives,” Industrial and Engineering Chemistry, J., 41, 1260 (1949).
Stamm, A.J., Thermal Degradation of Wood and Cellulose, Industrial and Engineering Chemistry J., 48, 413 (1956).
Rasch, R.H. and B.W.Scribner, “Comparison of Natural Aging of Paper with Accelerated Aging by Heating,” U.S. National Bureau of Standards Res. J., 11, 727 (1933).
Graminski, E.L., E.J.Parks and E.E.Toth, “The Effects of Temperature and Moisture on the Accelerated Aging of Paper,” ACS Symposium Series No. 95, 24, ACS, 1979.
Berry, G.M., S.P.Hersh, P.A.Tucker and W.K.Walsh, “Reinforcing Degraded Textiles, Part I,” Advances in Chemistry Series No. 164, 228, ACS, 1977.
Kerr, N., S.P.Hersh, P.A.Tucker and G.M.Berry, “Reinforcing Degraded Textiles: Effect of Deacidification on Fabric Deterioration,” ACS Symposium Series No. 95, 25, ACS, 1979.
Albeck, M., A.Ben-Bassat, and M.Lewin, “The Yellowing of Cotton Cellulose: Part II,” Textile Research J., 35(10), 935 (1965).
Section Index |