THE USE OF SPRAYED POLYVINYL ACETATE RESIN MIXTURES IN THE MOUNTING OF TEXTILES
Paul Himmelstein, & Barbara Appelbaum
ABSTRACT—A new method of treating various textiles, for which sewing is unsuitable, is described. Using a mixture of polyvinyl acetate resins AYAA and AYAC as a heat-seal adhesive, the textile is mounted onto a supporting fabric. The preparation of the adhesive-coated support is carried out using a spray gun. The treatment of a badly deteriorated 19th century silk American flag is described in detail. Steps include flattening, heat-sealing to a support, and final mounting inside a protective enclosure. Two variations in the use of polyvinyl acetate resins as a heat-seal adhesive are given. These involve the mounting of a painted Chinese silk and a printed silk square by Matisse. The physical flexibility achieved by spray application, the excellent aging and handling qualities of the resins used, and the safety provided by the final mounting package are discussed.
1 INTRODUCTION
There are certain textiles which for one reason or another, cannot be sewn, although, for those textiles which are physically strong enough, sewing is the least destructive and most easily reversible mounting technique. The fibers of many textiles are too deteriorated to take the strain put upon them by a sewing thread; the surfaces of some very smoothly finished textiles, usually silks, are too visually disturbed by sewing for this technique to be used. Various other methods have been devised for mounting textiles that cannot be sewn. Sandwiching textiles between a solid support and glass or Plexiglas is a common alternative, especially for pieces that do not require a great deal of manipulation during the mounting procedure. Methods of treatment which do not immobilize deteriorated textiles, including sewing between two layers of crepeline, do not provide adequate support.2
Various adhesives have been used to mount deteriorated textiles. Solvent adhesives3 (including aqueous ones) have some serious drawbacks both during and after treatment, which have been discussed elsewhere.4 Heat-seal adhesives offer many advantages, especially during the mounting process.5 One of these advantages is non-impregnation of the textile. This paper presents a heat-seal technique using a mixture of polyvinyl acetate resins that avoids many of the problems of earlier heat-seal procedures. Polyvinyl acetate resins retain greater solubility than the emulsions6 and, in the technique presented here, offer much greater flexibility of the mounted textile.
2 PROCEDURE
The general procedure described here was developed to treat a silk and cotton 34-star American flag measuring three by four feet and said to date from the 1860's. (The thirty-fourth state, Kansas, was admitted to the Union on January 1, 1861, and the thirty-fifth state, West Virginia, was admitted on June 20, 1863.) The flag was received tacked to a gold-colored cardboard laid over a piece of composition board and framed directly under glass. The silk of the stripes and field was extremely weak, brittle, and easily abraded, with many breaks. The stars were cut out of cotton and hand-sewn on either side of the field and were much stronger than the silk. There was extensive wrinkling and folding especially in the blue field, as shown in Figures 1 and 2. Because of the weakened condition of the fabrics and the smooth surface, the possibility of sewing was rejected. The flag clearly needed overall support to prevent further deterioration.
Fig. 1.
Detail of Flag Stripes Before Treatment.
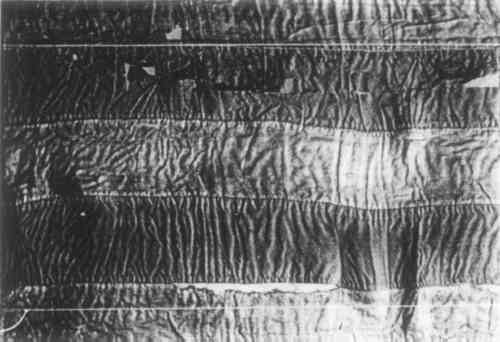 |
Fig. 2.
Detail of Flag Field Before Treatment.
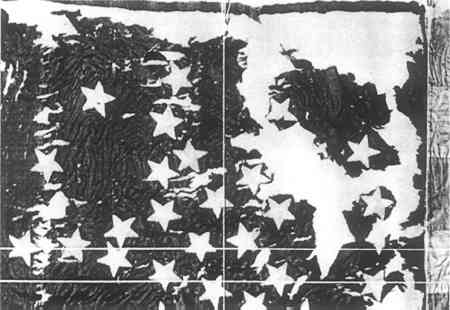 |
The tacks holding the flag to the cardboard were removed, and the cardboard was gently slid out from under the flag, leaving the flag on a piece of Kraft paper laid over Fome-cor. Threads to guide the blocking were stretched over the flag and secured to push-pins with rubber bands.7
The silk was blocked as follows: The fabric in the stripes was made more flexible by locally raising the humidity with a fine mist of water, and was then moved into position by careful manipulation. The red stripes were then further blocked and wrinkles taken out by ironing with a warm tacking iron through moist blotters. The white stripes, which were made from a more open-weave fabric, were too weak to withstand this procedure. The blue field was blocked as follows: One small area at a time (about two inches square or less) was relaxed with a fine water mist. Fragments were then unfolded and straightened with sable brushes and small spatulas. The area was then pressed under moist blotters and held flat with a square of Plexiglas and about one pound of weight. The blotters and weights were removed as each area was completely dry.
At the same time, a support fabric was prepared by stretching a length of silk crepeline net8 taut on a strainer. It was then sprayed from one side ten times over a period of two weeks with a ten percent solution of polyvinyl acetate resins (equal amounts of AYAA and AYAC) in toluene with a few drops of diacetone alcohol added to slow evaporation, sprayed at twenty-five pounds per square inch. The pressure was enough to assure that the fibers of the net were coated without the adhesive forming a continuous film between the threads.
[Since this treatment was carried out, we have changed this procedure slightly. We now dilute our 30% stock solutions (made in toluene) with ethanol and omit the diacetone alcohol. Spraying is done under the same conditions, but often no more than six times, depending on the weight of the textile.]
After several days of drying, the net was removed from the strainer and taped securely to glassine laid over a solid support. After the flag was transferred to the silk net and the threads were aligned as much as possible, the flag was attached to the net by ironing each area from the front with a warm tacking iron through glassine, as shown in Figures 3 and 4. The bond produced by the first application of minimal heat was weak enough so that the fragments could be removed by sliding a spatula under the fragment, and repositioning as necessary. After all the fragments were in place, the bond was strengthened by ironing with a larger tacking iron at a slightly higher temperature. At this stage, the iron was held for a longer time in each place. (This step could be carried out on a vacuum hot table, if one is available.)
Fig. 3.
Upper Right Corner of Flag Before Heat-Sealing to Net.
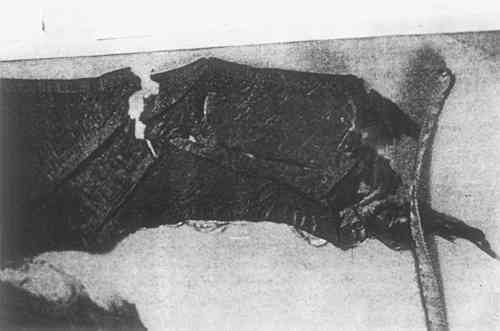 |
Fig. 4.
Upper Right Corner of Flag After Heat-Sealing to Net.
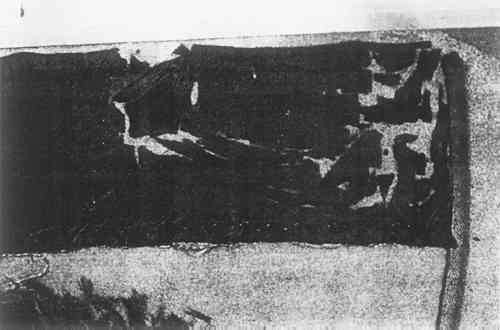 |
The final mounting was prepared by covering a wooden strainer with a one hundred percent cotton fabric,9 adhered with a polyvinyl acetate emulsion. The same fabric was also stretched to the thread across the back of the strainer. Fabrics chosen to match the colors of the blue field and white stripes were laid over the mounting fabric in the proper positions, with the blue over the white. The flag on its supporting silk net was laid over the colored cotton. All layers were secured to the mounting fabric by sewing along the original seams with a fine needle and soft cotton embroidery floss. The excess silk net and the edges of the background fabrics were trimmed to the edges of the flag. (The combination of the heat-seal support with sewing means that, in the future, the flag can be transferred to a new mounting without the need for retreatment of the flag.)
A five-sided box made of ultra-violet filtering Plexiglas (Rohm & Haas UF-3) was fitted over the front of the strainer and secured with screws into the sides, as shown in Figure 5. Acid-free lining paper (Talas) was laid over the back of the mounting fabric as a dust filter. A piece of quarter-inch thick pegboard with strips of the mounting fabric covering the edges was secured over the back by screwing into the strainer. This protects the back of the textile while allowing some circulation of air.
Fig. 5.
Flag After Final Mounting with UF-3 Plexiglas in Place.
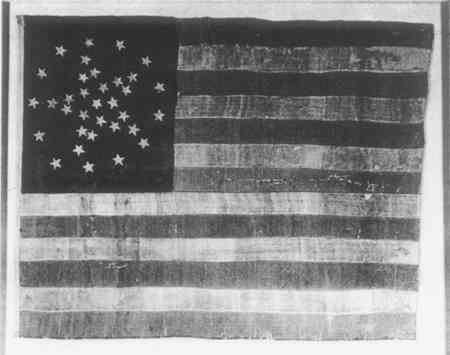 |
3 ADDITIONAL EXAMPLES
Two smoothly finished textiles, a nineteenth-century Chinese painted silk fragment, and a printed silk square by Matisse were treated using a similar technique. For the Chinese silk, a piece of cotton fabric was stretched on a temporary strainer and sprayed in much the same way as the crepeline. When a closed-weave fabric is used instead of a net, the spraying is done from a greater distance to form a web of dry adhesive on the surface and avoid impregnating the support fabric. The textile was attached to the cotton using an iron, working through glassine. After attachment, the mounting fabric was transferred to the front of a final strainer, and framed under UF-3 Plexiglas with a conventional ragboard mat.
The Matisse textile is in the form of a conventional scarf with rolled and hand-sewn edges. A cotton fabric was sprayed with resins as above, but with a larger proportion of AYAC in the mixture to lower the softening point, and therefore the temperature required for mounting. At the same time, a permanent mounting strainer was prepared as for the flag, with a colored cotton fabric covering the strainer and stretched behind it. The adhesive-sprayed cotton was then stretched behind the colored fabric with the adhesive adjacent to the colored fabric.
The scarf was laid in position over the colored fabric, and a pencil mark was made on the front of the colored fabric just inside the rolled edge. The scarf was removed, and the mounting fabric and prepared cotton were sealed together with a tacking iron, around the border up to the pencil line. The colored fabric was cut at the line and the center portion was removed, exposing an area of resin-coated cotton just smaller than the dimensions of the scarf. The scarf was replaced in position and secured with heat. Since the rolled edges of the scarf overlap the colored fabric and were therefore not attached by the adhesive, they were sewn down through both layers of cotton with single strands of cotton embroidery floss. The form of the rolled edges is still clearly visible. The package was finished in the same way as the flag and is shown in Figure 6.
Fig. 6.
Matisse Scarf After Mounting, with UF-3 Plexiglas in Place.
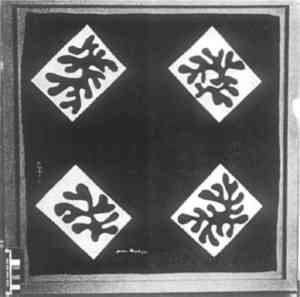 |
4 DISCUSSION
The method described above offers several advantages over previously described heat-seal mounting techniques. Polyvinyl acetate resin has been used by conservators for over forty years; its excellent aging and working properties are well known.10 Because it is available in several viscosity grades with different melting points, mixtures can be prepared with a wide range of softening points.11 The softening points of AYAC and AYAA are 89.6 and 150.8 degrees F. respectively. By changing the proportions of the mixture, and thereby the softening point, and by varying the application of heat, bonds of varying strengths can be obtained.
The actual exposure of the textile to heat is not severe. When using an equal mixture of AYAC and AYAA, on a silk embroidered textile being mounted to cotton, actual measurements were taken of the temperatures involved. The iron was set at around 140 degrees (measured with a surface temperature thermometer). Paper thermometers set at several places under the mounting fabric read between 110 and 120 degrees F. after the piece had been mounted. This compares favorably with the figure of 80 degrees C. (176 F.) given by Beecher for his heat-seal method using an internally plasticized vinyl acetate-vinyl caprate copolymer emulsion.12 The figure for the PVA heat-seal could be lowered further by changing the mixture.
Maximum flexibility combined with intimate overall support can be provided for extremely deteriorated textiles by using an adhesive-coated net. The use of a closed-weave fabric produces slightly less flexibility. The use of a sprayed rather than brushed or rolled layer of adhesive prevents the stiffening of the support fabric that would result if the threads were impregnated with resin. The resulting package, made up of the original and its support, retains all the qualities of a textile and can be mounted in a variety of traditional ways. Where complete immobilization is not necessary, the original plus support can be handled for display in the same way as the undeteriorated original.
Because the adhesive layer has very little gloss until ironed, it produces no visual disturbance in textiles with very open weave or sizeable voids. If the textile is mounted onto a fairly transparent net, general compensation can be carried out by laying a fabric of appropriate color under the net. If the textile is mounted onto an opaque fabric, the support itself can be colored appropriately.
If it becomes necessary to remove the textile from the support fabric, several alternative methods can be used. In the case of textiles which, like the Matisse scarf, are not deteriorated but have been heat-sealed for other reasons, the textile can simply be pulled away from the support, leaving no resin on the back of the textile. In other cases, toluene or other appropriate solvents can be sprayed onto the reverse of the support, and the support fabric can then be peeled away. If a hot table is available, heat can be used to reverse the mounting process.
The final mounting method used for the flag and the scarf was described in an article by the late Louisa Bellinger.13 It is excellent for textiles supported by either sewing or heat-seal adhesives. The textile is protected front and back from dust, mechanical damage, and ultraviolet light, without being completely sealed off from the outside environment. Constant tension is maintained throughout the treatment procedure, since the fabric supporting the textile does not have to be transferred to a second support for display. At the same time, the textile remains easily accessible for further treatment, cleaning of the Plexiglas, etc. The Plexiglas is automatically held away from the textile without additional liners or spacers being needed. If desired, a window can be made on the mounting fabric to allow viewing of the reverse of the textile. The whole package can also be inserted into a conventional frame.
We feel strongly that it is a conservator's responsibility to see the treatment of a textile through to a point where the textile is safe from careless handling. The proper mounting of a textile onto an auxiliary support, regardless of the method, cannot in itself insure the future safety of the original. If nothing remains to be done to permit display, then the textile is that much safer from framers, museum technicians, and other personnel who are often untrained in the special problems of textiles. The final mounting package we have described assures that this is the final result and provides the additional protection required for the preservation of the object.
This heat-seal technique, as all previously described heat-seal methods, is only suitable for thin textiles. Because there is attachment only to the back layer of fibers, with thicker textiles there would be a tendency for separation to occur at points of stress between adhered and unadhered fibers. This is especially true of multi-layered textiles such as Paracas embroideries. In some special cases, sewing can be combined with a heat-seal method.
While the use of sprayed polyvinyl acetate resins is not suitable for certain types of textiles, it is adaptable to a wide range of textile conservation problems and can be combined with sewing where appropriate. In the past, the spray gun generally has been used by paintings conservators. Like the vacuum hot table, which was developed for the treatment of paintings, but has been used successfully in the treatment of textiles,14 the spray gun may prove to be an extremely useful tool in textile conservation. It is very important for conservators in a particular specialty to familiarize themselves with the techniques and tools of other specialities, so that in the future they may have the widest possible range of treatment techniques at their disposal.
REFERENCES
Partners, Appelbaum and Himmelstein, 444 Central Park West, New York, New York 10025. Ms. Appelbaum is also Assistant Conservator at the Brooklyn Museum.
Lehmann, Detlef, “Conservation of textiles at the West Berlin State Museums,” Studies in Conservation9 (1964), p. 19.
Those adhesives which are applied in a volatile solvent and set as the solvent evaporates.
Leene, J. E., ed., Textile Conservation, Butterworths, London (1972), pp. 144–151.
Berger, Gustav, “Formulating Adhesives for the Conservation of Paintings,” Conservation of Paintings and the Graphic Arts (Preprints of Contributions to the Lisbon Conference), I.I.C., London (1972), pp. 613–629. See especially figures 3 & 4 and accompanying legends.
Phelan, W. H., Baer, N. S., Indictor, N., “An Evaluation of adhesives for use in paper conservation,” Bulletin of the American Group of I.I.C.11 (1971), pp. 58–75.
Scott, K., “Conservation of a Paracas Mantle,” Bulletin of the American Group of I.I.C.10 (1970), note, p. 159.
In the future, we would probably substitute a polyester net very similar to crepeline, available from Talas.
All cotton fabrics were washed several times in hot water before use.
Gettens, R. J., “Polymerized Vinyl Acetate and related compounds in the restoration of objects of art,” Technical StudiesIV (1935), pp. 15–27.
Rabin, B., “A Poly (vinyl acetate) heat seal adhesive for lining,” Conservation of Paintings and the Graphic Arts (Preprints of Contributions to the Lisbon Conference), I.I.C., London (1972), pp. 631–633.
Beecher, E. R., “The Conservation of Textiles,” The Conservation of Cultural Property, p. 262, UNESCO, Paris (1968).
Bellinger, Louisa, “The Cleaning of textiles,” Delft Conference on the Conservation of Textiles, pp. 92–93, I.I.C., London (1964).
Scott, K., “New Treatment for an old textile problem,” Bulletin of the American Institute for ConservationXIV (1974), pp. 168–170.
Section Index |