CONSERVATION OF A FAN
SANDRA GREENWALD VIERRA, & BETHUNE GIBSON
ABSTRACT—The treatment described was primarily a problem in textile conservation, although the fan is composed of silk, metal, and ivory. The major difficulty encountered was the extreme fragility of the embroidered silk panel. Reversible materials were used as far as possible, although in practice these would be difficult to remove without destruction of much of the silk. The methods used are not all new but their application here is of interest because of the complexity of the problem and the urgent need for consolidation of objects made with similar materials. The fan was strengthened and restored to a point where it can now be handled, studied, and exhibited under proper conditions.
1 HISTORY
In 1876 a silk, embroidered fan was among the articles sent from Thailand (then Siam) to the United States for exhibit in the Centennial Exhibition, which was held in the U.S. Government Building in Philadelphia from May to November 1876. According to the 1876 Smithsonian Annual Report, the objects were made expressly for the exhibit. The date of manufacture is thus established with reasonable accuracy, and the damage sustained over the 100-year period of exposure may be strikingly demonstrated.
Photographs of the 1876 exhibits illustrate the manner in which the objects were displayed; the majority were placed on tables unprotected by cases and often piled in more or less random fashion. Lighting was mostly natural sunlight through large windows extending around the upper walls of the room. An average of 62,000 people arrived per day to see the exhibit.
In December of that year all specimens were crated and sent in twenty-three box cars to Washington, D.C., to be stored in a warehouse. In February 1881, the Arts and Industries Building opened, exhibiting some of these objects. Records do not indicate whether the fan was among them; if not, it was either left in storage in the original warehouse or recrated and placed in another warehouse. Neither temperature nor humidity controls were present in either location.
Later, some of the material was stored in wooden drawers in the National Museum of Natural History at the Smithsonian Institution, where, again, no climate control existed. Renovation of this building took place over a long period, ending in 1964 when an air-conditioning system was completed. At this time the Southeastern Asian Collection was transferred to a wing with proper humidity and temperature controls.
In 1975 the fan was discovered during an inventory of the collection, lying in a pine drawer unprotected by any packaging or wrapping. The metal storage unit containing the drawers was, however, reasonably air tight as a close-fitting cover over the front protected the contents from dust and most airborne pollutants.
2 DESCRIPTION
The fan shown in Figure 1 is composed of two layers of silk between which is a supporting frame of brass spokes soldered to an ovoid, flat rim. The frame fits into a slot at the top of a handle cut from a single piece of ivory 23″ long by 1″ wide. Both ends of the handle are carved.
Fig. 1.
Drawing of fan and frame.
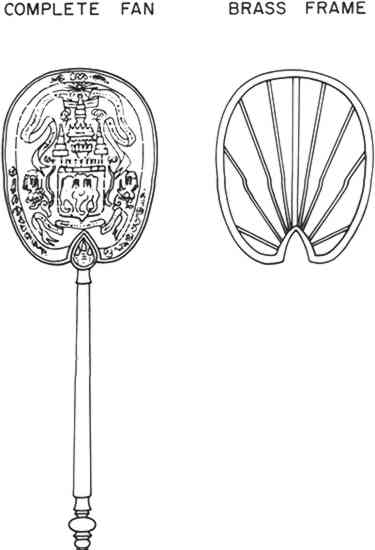 |
The silk panels are bound to the frame by a braid of black, yellow, and metallic silver threads. The front panel is elaborately embroidered in a satin stitch with multi-colored silk threads and outlined with metallic silver thread. The large central design represents the royal coat of arms of the King of Siam. The back panel is made of salmon pink brocade with a glossy surface. Alternating flower patterns are woven into the fabric.
3 CONDITION
3.1 Front Panel
The silk was very deteriorated, with numerous broken threads and many areas of loss between the embroidery units. The embroidery was in good condition, except for a few loose silver threads outlining the design. Fading, however, was severe. When the panel was removed from the frame the inner surface revealed the original Prussian blue, which had faded on the exterior surface to a pale green. The embroidery, which had been stitched in several shades of orange and ivory, had become a uniform cream color. The causes of deterioration must be deduced from our meager information concerning the fan from its arrival in the United States to the day it was found in a storage unit in the National Museum of Natural History. While on exhibit in Philadelphia, unprotected by a case, the fan was exposed to sunlight from the windows, handling and contact with other objects, dust particles and air pollutants. In addition, uncontrolled humidity and temperature would have enhanced the deterioration of the silk. The sunlight provided heat as well as exposure to ultraviolet light, which must have caused most of the fading. The storage conditions during the years following exhibit furnished darkness, but little additional protection. Other environmental factors during this period are unknown.
3.2 Back Panel
The silk of this portion was in much better condition probably because it would have been the side that was not exposed to direct light when on exhibit. Fading was moderate, but the surface was quite dusty from contact with exhibit and storage surfaces. There were three small holes in the fabric, caused by abrasion from bent spokes of the frame.
3.3 Braid Edging
This binding was a type of woven braid in which black, yellow, and tarnished, black silver threads predominated. Some of the silver threads were composed of yellow thread wrapped with a thin strip of metal. In addition, a thin silver strip 1.5 mm wide was woven into the braid and it also was black with sulphide corrosion products. The braid seemed to be relatively sound before disassembling the fan, but when the panels and braid were separated from the metal rim of the frame, the edging proved to be very weak, with the weft threads breaking easily. Since the braid had to be removed by softening the adhesive that bound it to the fan, this separation action loosened some of these delicate weft fibers.
4 EVALUATION OF THE PROBLEM
All decisions regarding treatment were not made before work was begun, partly because all of the problems were not revealed until the fan was disassembled. It was evident, however, that the silk of the embroidered panel needed consolidation, that both it and probably the brocade panel would require backing with a silk of the same weight and that the consolidated panel might need the addition of a facing of crepeline to protect it from handling contact in the future.
5 TREATMENT
Both sides of the fan were photographed in color and in black and white and are shown in Figures 2 and 3. A sample close-up photo made to show the amount of deterioration of the silk is shown in Figure 4. Other photographic records were made during the conservation process.
Fig. 2.
Front panel before conservation.
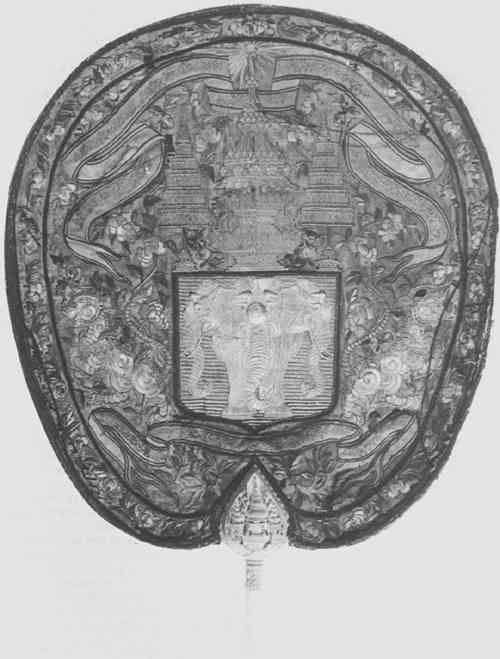 |
Fig. 3.
Back panel before conservation.
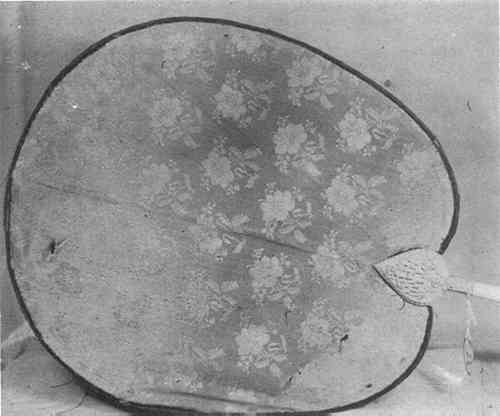 |
Fig. 4.
Close-up of deterioration before disassembly.
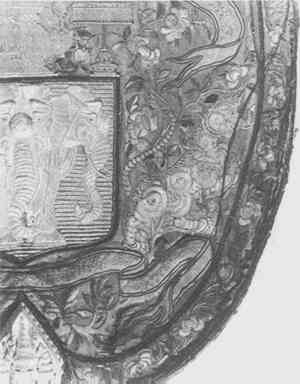 |
The edging braid was removed by cutting the cotton thread that secured it with a thin, sharp scalpel. In addition, the panels were found to be fastened down with a yellowish adhesive that softened slightly when tested with a cotton swab dampened with water. This, however, tended to spot the silk. Ethyl alcohol was then used, and as this easily removed the adhesive, it was assumed to be shellac or a similar natural resin. As the adhesive was dissolved, the edges of the panel were separated with a dental pick and a small spatula. When the panels were removed from the frame, the original color of the silk was revealed. As a matter of interest, the blue dye was tested by removing a few threads of the silk and applying dilute sodium hydroxide. This produced a bleaching action; after application with dilute hydrochloric acid the color returned. This indicated an acid dye. Elisabeth West Fitzhugh, of the Freer Gallery of Art, also tested a sample with the same result.3
Next, a wooden frame was constructed measuring 21-1/2″ wide by 27″ long. Pale green China silk was stretched over it and tacked to the edge, using just enough tension to support the front panel smoothly without sagging. The warp and weft threads of the old silk were aligned with the backing as closely as possible. The panel was stitched to the backing using a very fine white silk thread that was split into four threads, making the stitches nearly invisible. The needle used was short and fine, with an eye so small that a magnifier was used to thread it.
Starting at the center, each embroidery element was stitched down along its edges, using a minute stitch on the right side and a long one on the under side. The embroidery was so extensive and covered such a wide area that it was not necessary to sew into any of the fragile silk, which would not have supported stitches in any case.
The background silk was almost the consistency of paper ash, breaking under any but the slightest touch. Even with the most careful handling, there was some unavoidable loss in mounting the panel on the backing. It was clear that impregnation with a consolidant was necessary. Ethulose 4004 (soluble in water and ethanol) was tentatively chosen because, in our experience, of its successful use on other fabrics, because of its reversibility (although in this case reversibility would not be possible without destructive results), and because of the mild solvents in which it could be applied.
The colors of the embroidery were tested for bleeding in both water and ethanol. The oranges and yellows bled very slightly in ethanol and the green in water. Therefore, it was decided to impregnate the plain silk first and dry it; then the embroidery could probably be impregnated without danger of the embroidery colors bleeding into the silk. A solution of Ethulose 400 was made by dissolving the Ethulose in 2:3 distilled water to ethanol. Tests were made on scraps of the China silk backing for changes of color and flexibility. These were found to be quite satisfactory, and the impregnation of the silk and the embroidery was carried out as planned, on a very small area to observe the results. No bleeding occurred, so the remaining areas were treated with complete success.
This process did not adhere the silk of the panel to the backing and was not intended to do so. The solution was applied with a very small artist's brush and dripped gently onto the surface. The silk absorbed the liquid immediately. When the panel was dry, it was faced with an off-white crepeline. Stitching was done with the same silk thread, and the facing was attached around the edges of the embroidery and around the edges of loss areas to prevent shifting of the old silk. This last stitching was made through the crepeline and backing only, so that the needle did not penetrate the old silk at any point. The completed panel shown in Figure 5 was then treated again with Ethulose applied to the same areas as before. The solution was the same concentration, with the addition of two drops of Carbowax 4003 to each five grams of solution for increased flexibility. This was thought advisable because when remounted, the fan would be under some tension. Allowance was therefore made for slight expansion and contraction due to humidity changes in an uncontrolled storage climate. Due to the thickness of the embroidery, the crepeline did not lie directly on the surface of the old silk, therefore, the Ethulose solution could be dripped through the crepeline, which was then blotted dry with lab tissues. When dry, the panel was removed from the wooden frame and the silk backing was trimmed, leaving a 1.3 cm margin that was folded under and tacked down with silk thread. The completed treatment of the embroidered panel is shown in Figure 6.
Fig. 5.
Completed panel, detail.
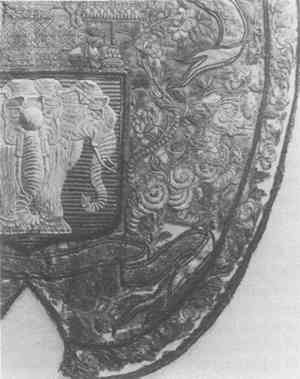 |
Fig. 6.
Embroidered panel, completed
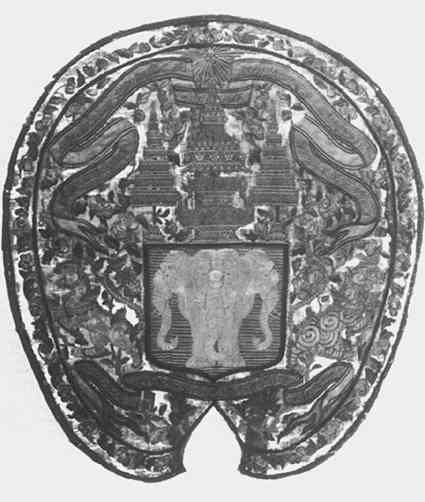 |
5.1 Back Panel
The panel of pink brocade was placed on a white blotter and the heavy deposits of resin along the edge were removed with ethanol and cotton swabs. Since this panel appeared to be much stronger than the embroidered one, it was possible to secure it between two pieces of nylon screen and wash it with distilled water and Orvus.4 It was rinsed in three changes of distilled water and suspended on the screen for air-drying. Following this it was attached to a backing of the same China silk and sewn down with the same silk thread, working from the center outward. No impregnation or facing of this panel was considered necessary.
5.2 Braid
The braid was in such delicate condition that it was necessary to support it with a double backing of crepeline before it could be used to rebind the fan panels to the rim of the frame. The crepeline was attached with Beva 3715, by melting it with a tacking iron set at medium heat.
5.3 Frame
The brass frame was covered with a layer of thin corrosion products. Three spokes needed to be straightened; one had been cut originally to an incorrect length for its position in the frame, causing it to bend. For some reason this had not been noticed when the fan was being assembled. The brass was cleaned with Noxon metal cleaner on cotton swabs and thoroughly rinsed with distilled water. Noxon is not normally used to clean copper alloys because of the possibility of undesirable reactions of the copper with the ammonia in the cleaner. However, in this case the metal was perfectly smooth and there was so much polishing following the removal of the corrosion products that it seemed reasonable to assume that the ammonia would be completely removed before any damage could occur. Cleaning was followed by rubbing with steel wool, grade 0000. A felt-tipped accessory wheel on the flexible high-speed machine accomplished the final polishing. The frame was then coated with Acryloid B-726 in acetone and dried. It may be noted that the metal was restored to a high polish, as the original glossy surface was evident beneath the corrosion products in some areas.
The bent spokes were straightened with a screwdriver; the over-long one was recut and resoldered to the rim.
5.4 Ivory Handle
This was in good condition, except for two hairline cracks along the shaft. The grime was removed with spirit soap and small cotton swabs, and the entire handle was rinsed with ethanol.
6 REASSEMBLY OF UNITS
The two panels were glued to the frame edges with polyvinyl acetate emulsion, Talas R-1317. The braid was attached to the edge using nylon thread for additional strength. The stitch was loose enough so that the material would not be cut by the nylon, which was unlikely in any case because of the layers of new silk and crepeline at the rim. The edges of the braid were lightly glued to the panels with R-131 so that they would lie flat.
The completed fan was then joined to the handle and packaged for storage. The blade of the fan was enclosed in a 4 mil polyethylene bag, then in an envelope of medium weight white paper board for further protection. The handle was encased in a tube of polyethylene of the same weight.
7 SUMMARY
As stated at the beginning, this object was in urgent need of treatment. Minimum conservation was impossible, as the fragility of the materials was extreme. Undoubtedly, the methods used were not the only ones that could have been chosen, but the conservator made the choices that seemed to her to be the best for this particular specimen. It may be of interest that the work on the fan, including research on its history and the small amount of documentation available, occupied nearly four months, an estimated 640 hours of work time.
REFERENCES
Sandra Greenwald Vierra, 35, anthropologist and ethnographic conservator, died August 1975. She had just completed her conservation training and had been appointed conservator at the Pacific Regional Conservation Center in Honolulu, Hawaii. She had planned to publish her conservation of the fan in the near future. It is presented here by Bethune Gibson, a friend and one of her teachers, as a memorial to a fine conservator whose promising career was cut short so tragically.
Head Conservator, Anthropology Conservation Laboratory, National Museum of Natural History, Smithsonian Institution, Washington, D.C. 20560
Personal communication, Elisabeth West Fitzhugh, Freer Gallery of Art, Dec. 3, 1975. “The blue color of the silk fiber disappears immediately on application of 5% NaOH, and when dilute (1:4) HCL is added, the blue color returns. This behavior is a strong indication that the blue color is supplied by Prussian blue.”
Ethyl-hydroxyethyl cellulose (equivalent to Modocoll E), Chemaster Corp., Long Island City, N.Y. 11101
Carbowax 400 (polyethylene glycol 400). Union Carbide Corporation, New York, New York 10017.
OrvusWA, a non-ionic detergent.
B-371, a heat-activated adhesive composed of a mixture of resins, paraffin, and low-aromatic petroleum solvents. Adam Chemical Co., P.O. 15, Spring Valley, N.Y. 10977.
Acryloid B-72 is an ethyl methacrylate copolymer. Rohm & Haas, Independence Mall West, Philadelphia, Pa. 19105.
See the Talas catalog for 1975, p. 27. R-2258, a PVA emulsion, is now a substitute for R-131.
ACKNOWLEDGEMENTS
The compiler is greatly indebted to Elisabeth West Fitzhugh of the Freer Gallery of Art, Smithsonian Institution, Washington, D.C., for making the confirming chemical test to determine the type of the blue dye of the embroidered panel. Thanks are also due to Joan E. Gardner, ethnographic conservator, for her assistance in the research on the history and travels of the fan; to Joseph V. Columbus, textile consultant, for providing the silk thread and needles for sewing the fan to the backing; and to Carolyn L. Rose for assistance in assembling the manuscript. Photographs of the fan, except Figure 4, were made by the staff of the Smithsonian Photo Laboratory.
Section Index |